
Train logistique, tremplin vers les systèmes de transport automatisé ?
Un train logistique est un système de transport utilisé pour déplacer de grands volumes de marchandises entre différentes zones de l’entrepôt.
Toutefois, dans certaines installations logistiques ou centres de distribution gérant d’importants flux entrants et sortants, cette solution peut s’avérer insuffisante. Dans ce cas, il est recommandé de remplacer les équipements de manutention manuelle par des systèmes de transport automatique tels que des convoyeurs pour palettes ou des systèmes monorails.
Qu’est-ce qu’un train logistique ?
Un train logistique est un équipement de manutention composé d’un tracteur conduit par un opérateur et d’un ensemble de remorques reliées au tracteur avec une capacité de charge individuelle pouvant atteindre 2000 kg. Généralement, il est utilisé pour accélérer le déplacement des stocks sur des distances supérieures à 100 mètres, ce qui dynamise le flux de marchandises entre deux postes de travail éloignés.
Ces systèmes de transport logistique se distinguent par leur polyvalence. Les remorques proposent différentes configurations qui s’adaptent à tous les besoins. De cette façon, ils peuvent déplacer tous les types de charges au sein d’un entrepôt, des palettes, des bacs, des grands conteneurs, des pièces ou des pneus.
Ces engins sont également disponibles dans une configuration AGV avec système de navigation filoguidé, dans laquelle le tracteur et les remorques sont conservés, mais la commande de la machine est automatisée par l’installation d’un câble qui émet un champ magnétique sur le sol de l’entrepôt. Le câble signale la trajectoire à suivre par le tracteur.
Avantages (et inconvénients) d’un train logistique
Un train logistique est un équipement de manutention similaire à un chariot élévateur, mais contrairement à ce dernier, il peut déplacer un plus grand nombre de palettes en un seul trajet, car le tracteur est capable de tirer plusieurs remorques simultanément. C’est un avantage certain par rapport à d’autres équipements de manutention, généralement limités à la manutention d’une seule unité de charge logistique à la fois.
Comparée aux transpalettes ou aux chariots élévateurs, cette solution permet :
- Transport de grands volumes de marchandises : un train logistique permet de déplacer un grand volume de marchandises entre différentes zones de l’entrepôt ou entre deux postes de travail, il peut être conduit par un opérateur ou au moyen d’une machine avec système de navigation filoguidé.
- Flexibilité dans la manutention des charges : les trains logistiques sont composés d’un tracteur et d’une combinaison de différentes remorques, qui varient en fonction des besoins de chaque client. La configuration des remorques est très variable, elle comprend des modules adaptés aux palettes européennes conventionnelles, à d’autres dotés d’un portique pour déplacer des marchandises stockées verticalement.
- Sécurité et ergonomie : ces machines sont équipées de dispositifs antidémarrages, c’est-à-dire de dispositifs de sécurité qui empêchent le mouvement du train lorsque les remorques ne sont pas correctement positionnées ou relevées. En outre, les mécanismes de levage fonctionnent avec contacteur au pied pour améliorer l’ergonomie et pour une conduite plus intuitive pour l’opérateur.
Toutefois, cette solution peut s’avérer inefficace face à une hausse du volume d’entrées et de sorties de marchandises dans l’entrepôt. Bien que la capacité de charge d’un train logistique soit considérable, elle est néanmoins limitée, et le flux de marchandises qu’il permet est toujours unidirectionnel, ce qui est un inconvénient lorsque des niveaux élevés de productivité sont exigés.
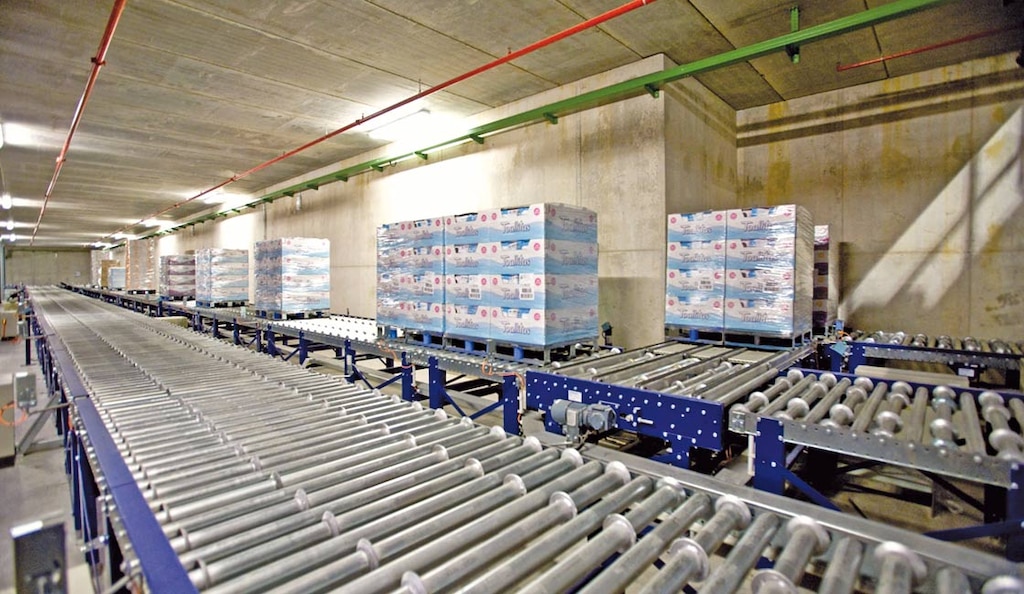
Les trains logistiques vs les convoyeurs automatiques
La principale différence entre un train logistique et un convoyeur industriel est le volume de produits déplacé simultanément. Alors que la capacité de charge d’un train logistique est limitée à l’ensemble des remorques qui le composent, des systèmes tels que des convoyeurs pour palettes ou des convoyeurs pour bacs sont conçus pour déplacer un plus grand volume de marchandises en continu.
Les convoyeurs offrent un environnement de travail plus sûr : les cloisons industrielles grillagées séparent et protègent les opérateurs des machines, ce qui préserve l’intégrité du système et de la charge. Toutefois, les entrepôts dans lesquels sont utilisés des trains logistiques, qu’ils soient conduits par un opérateur ou filoguidés, doivent clairement signaler l’itinéraire emprunté pour éviter les risques de heurts et les accidents, car les trains logistiques circulent dans la même zone de travail que les opérateurs.
Les convoyeurs et les trains logistiques ont une caractéristique commune qui est leur flexibilité, car ils ont tous deux une large gamme d’accessoires qui permettent de configurer des circuits complexes, adaptables au layout (ou agencement) de l’entrepôt et modulable selon les besoins des clients. En revanche, les trains logistiques filoguidés peuvent parfois obliger les entreprises à revoir l’organisation de leur entrepôt afin de marquer les itinéraires empruntés à l’intérieur et à l’extérieur de l’installation. Face à la nécessité de programmer des itinéraires, les convoyeurs pour palettes sont une solution plus productive et plus économique : ils peuvent transporter des volumes plus importants de marchandises sur un même itinéraire et ne nécessite qu’un minimum d’entretien.
En effet, les circuits de convoyeurs peuvent comprendre des modules à rouleaux, à chaînes ou mixtes, en fonction des mouvements requis pour le transport des palettes. En outre, ils proposent des configurations simples, telles que le plug & play, qui se caractérise par une grande facilité de montage puisqu’il ne nécessite aucune programmation. Il existe également des éléments plus complexes, comme des tables hydrauliques, des élévateurs de palettes ou des butées de palettes, entre autres.
De plus, alors que le train logistique ne sert qu’au transport de marchandises entre deux postes de travail situés au même niveau, les convoyeurs permettent d’accumuler les charges ou de les déplacer entre différents niveaux dans l’entrepôt.
Pour ces raisons, le convoyeur à palettes est la solution idéale pour un entrepôt proche des lignes de production. C’est le cas du nouvel entrepôt de Císter au Portugal, où cette solution de transport automatique garantit un flux continu entre les lignes de production et l’entrepôt où est stocké le produit fini, sans qu’il soit nécessaire d’affecter un opérateur à la circulation des marchandises. Le logiciel qui coordonne le convoyeur déplace la marchandise qui sort des lignes de production et lui attribue un emplacement dans l’entrepôt automatisé. Ce flux automatique des marchandises évite les goulets d’étranglement aux sorties des lignes de production.
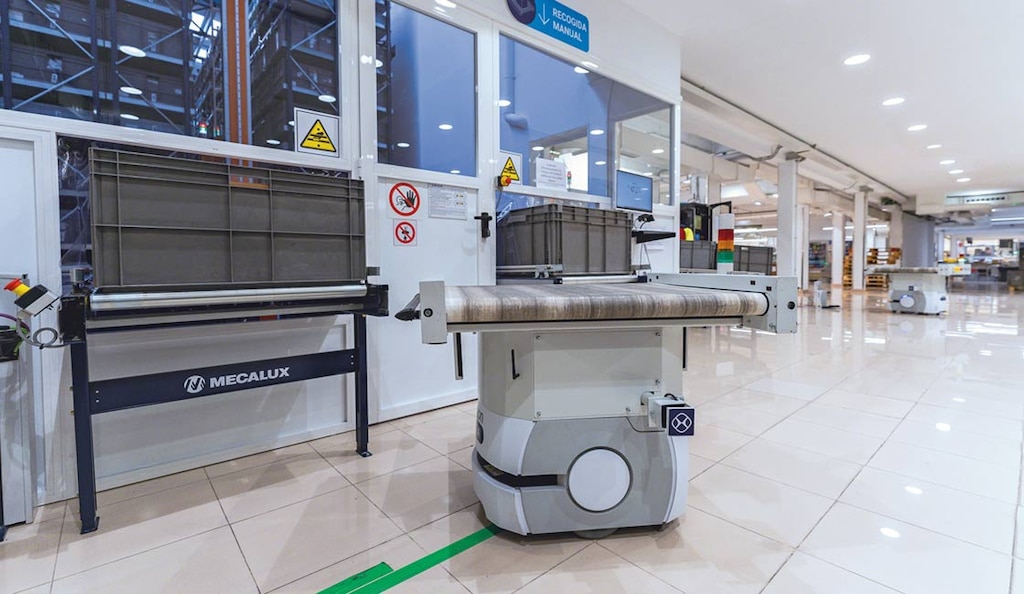
Les trains logistiques vs les robots AMR
En tant que système de transport de marchandises, le train logistique peut également être comparé à des robots mobiles, également connus sous le nom d’AMR, abréviation de Autonomous Mobile Robots. Ces machines se déplacent et transportent des marchandises de manière autonome dans l’entrepôt, sans devoir prédéfinir de circuit. Un système de commande, intégré dans le logiciel de gestion d’entrepôt, pilote les mouvements du robot.
Contrairement aux trains logistiques, ces robots sont généralement programmés pour transporter des charges moins lourdes, bien qu’il existe également des modèles conçus pour le transport de marchandises palettisées. Par exemple, ils sont utilisés dans les entrepôts d’e-commerce ou dans des secteurs tels que la logistique pharmaceutique, qui travaille avec des produits de petite taille.
Cependant, les robots AMR, bien qu’ils soient en constante évolution, ne disposent pas d’une technologie consolidée telle que les systèmes de transport automatique. Cela implique que leur mise en œuvre dans un entrepôt nécessite encore un investissement important, soit pour l’acquisition de machines, soit pour des licences d’utilisation périodiques.
Le train logistique : une solution simple à un problème complexe
Les trains logistiques sont une solution de transport qui peut se révéler efficace lorsque l’on souhaite rationaliser la circulation des marchandises, mais seulement dans certains contextes. Après tout, ils sont une évolution naturelle du transport de marchandises par transpalette, un engin de manutention manuel traditionnellement utilisé pour le chargement et le déchargement des camions.
Cependant, il existe sur le marché des solutions de transport automatique plus efficaces qui garantissent avant tout une productivité maximale de l’approvisionnement des postes de travail ou des lignes de production. Les systèmes tels que les convoyeurs automatiques sont une solution flexible et adaptable aux exigences de tout entrepôt, rationalisant complètement la circulation des marchandises dans toute l’installation.
Si vous souhaitez optimiser la productivité de votre installation, n’hésitez pas à nous contacter. Notre équipe d’experts analysera les performances logistiques de votre entrepôt et vous proposera une solution adaptée à vos besoins.