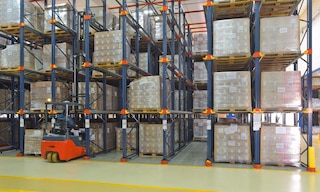
Honeycombing dans les entrepôts : de quoi s’agit-il et comment le réduire ?
Le phénomène d’honeycombing ou nid d’abeille, dans les entrepôts, désigne la perte de capacité de stockage effective suite à un excès d’emplacements vides qui, en pratique, ne peuvent pas être utilisés parce qu’ils sont réservés à certaines références. Cette situation est courante lorsque le critère d’affectation des emplacements est inflexible, comme c’est le cas avec certains systèmes de stockage compacts. Si les unités de charge sont retirées et qu’il n’y a pas assez de stock de la même référence pour remplir les emplacements vides, il n’est pas possible d’y placer une référence différente pour occuper les espaces libres.
Il existe des solutions logistiques qui atténuent les conséquences du warehouse honeycombing dans les entrepôts où ce phénomène se produit. Nous allons voir dans cet article les solutions à mettre en place pour résoudre ce problème.
Qu’est-ce que l’honeycombing warehouse ou nid d’abeille en entrepôt ?
En anglais, le warehouse honeycombing, également connu sous l’effet nid d’abeille, désigne l’espace vide laissé dans le rayonnage qui ne peut pas être utilisé pour stocker une autre référence et qui est directement lié à la perte de capacité de stockage effective. Il peut apparaître dans les entrepôts appliquant une stratégie d’affectation des emplacements fixe (par opposition au stockage dit banalisé ou chaotique) ou dans ceux équipés de systèmes de stockage compacts, tels que les rayonnages par accumulation drive-in, lorsqu’ils sont utilisés dans des installations qui ne répondent pas aux besoins de l’entreprise. Si l’alvéole vide, mais non disponible, apparaît en hauteur, elle constituera un alvéolage vertical et si elle apparaît en profondeur, ce sera un alvéolage horizontal.
Prenons l’exemple des rayonnages drive-in, un système dans lequel une même référence est stockée sur toute la hauteur et la profondeur de l’allée de stockage. Le nid d’abeille se produit lorsque des emplacements sont libérés dans cette allée (mais pas tous) et que la nouvelle unité de charge à stocker ne correspond pas à cette référence. Il en résulte une perte temporaire d’espace de stockage. Face à cette situation, certaines entreprises choisissent de mélanger des références dans une même allée, mais cela complique les opérations, car pour accéder à certaines palettes, il faudra d’abord en retirer d’autres.
Dans les entrepôts appliquant une stratégie d’affectation des emplacements fixe, la perte d’une certaine capacité de stockage est inévitable, et le nombre d’unités stockées est inférieur à la capacité globale de l’installation. Cependant, même si la capacité de stockage est perdue, l’exploitation de l’espace peut être supérieure à celle obtenue avec des systèmes de stockage à accès direct et sans alvéolage. C’est-à-dire que, dans certaines conditions, une configuration avec alvéolage ou nid d’abeille, peut être préférable à une configuration sans ce phénomène.
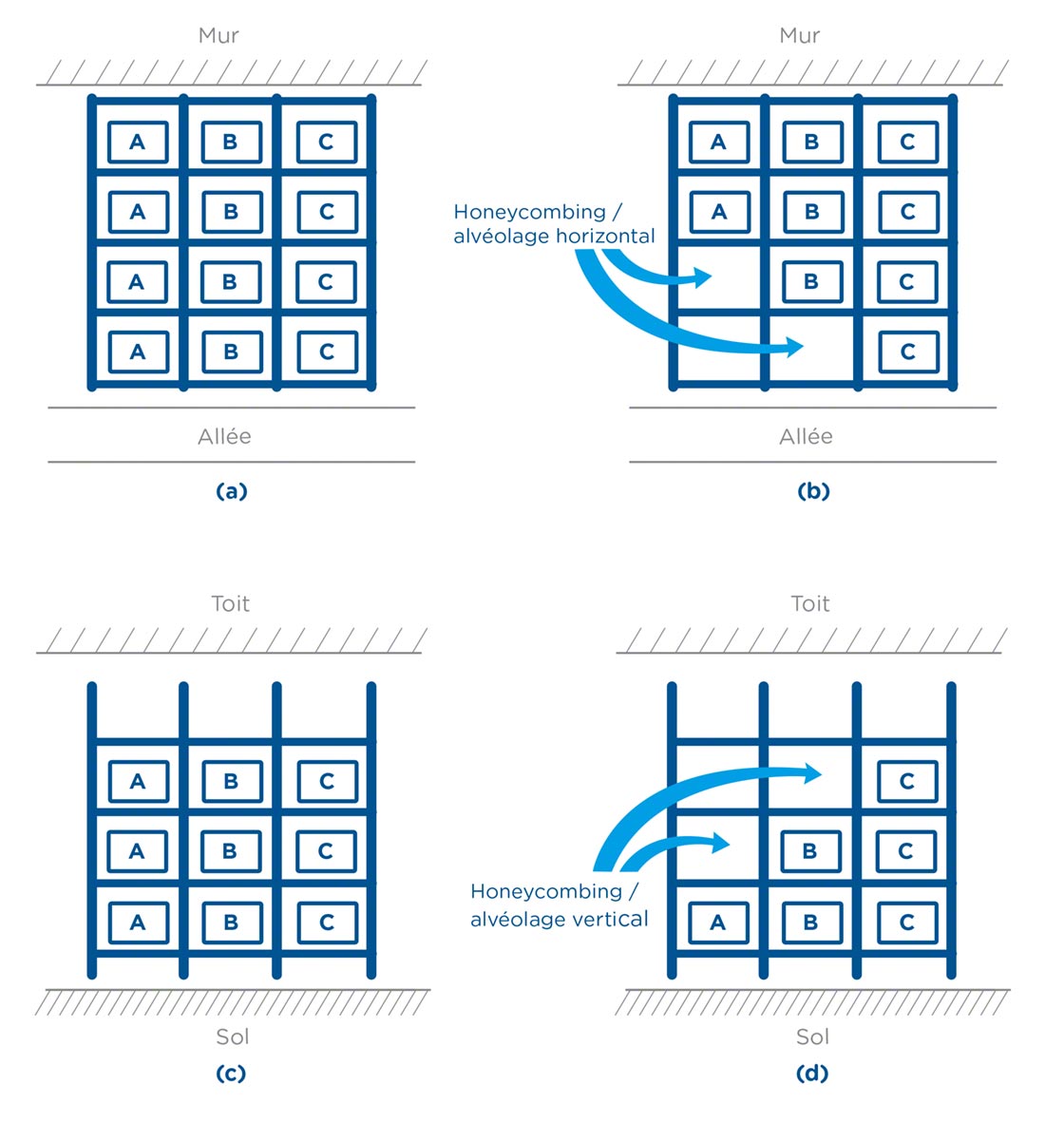
Les causes du honeycombing
L’honeycombing dans les entrepôts peut avoir de nombreuses causes, parmi lesquelles :
- Stratégie d’emplacement des produits : si un critère ou une règle d’affectation d’emplacement fixe est appliqué (c’est-à-dire que les références sont toujours stockées au même endroit), cela peut entraîner un nid d’abeille, car lors du réapprovisionnement, les marchandises ne correspondent souvent pas aux emplacements disponibles pour chaque référence.
- Mauvaise gestion d’entrepôt : le manque d’organisation en matière de stock management est l’une des principales raisons de l’apparition de l’effet nid d’abeille. Cela peut générer des pertes de stock qui empêchent la bonne gestion des emplacements de stockage, créant des espaces vides non exploités par méconnaissance. Ce phénomène peut également se produire lorsque les marchandises sont mal placées.
- Erreur de palettisation : une erreur dans le processus de palettisation peut impliquer des erreurs lors du stockage des marchandises. En effet, lorsque la charge dépasse les limites de la palette ou qu’elle est empilée de manière irrégulière, il est possible qu’un espace de stockage vide soit créé et ne puisse pas être utilisé.
- Profondeur de canal : les systèmes de stockage de grande profondeur présentent un plus grand risque d’honeycombing horizontal, en particulier lorsque la méthode d’extraction de produit LIFO est appliquée ― le premier produit entré est le premier sorti ―.
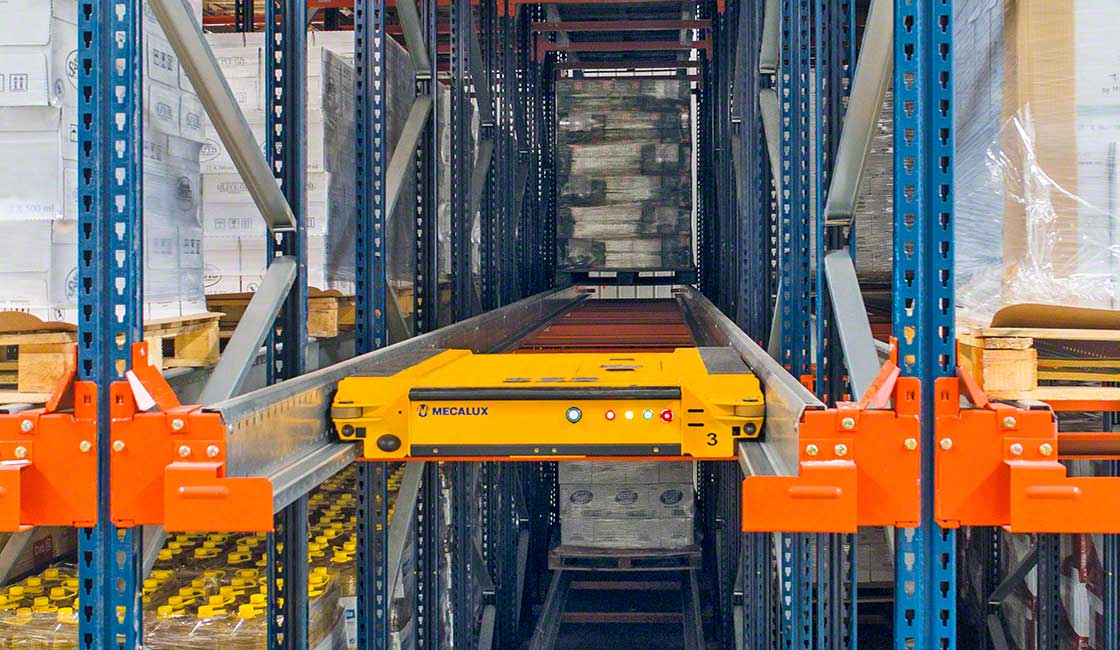
Comment évaluer l’effet d’honeycombing warehouse ?
La perte de capacité effective dans les entrepôts due à l’effet nid d’abeille peut être calculée à l’aide de la formule suivante :
Capacité effective (%) = (espace en mètre cube utilisé / capacité de stockage totale) x 100 = (nombre d’emplacements occupés) / (nombre total d’emplacements) x 100
Cette formule indique le pourcentage d’espace de stockage occupé à un moment donné par rapport à la capacité maximale de l’entrepôt. Pour avoir une idée plus précise de l’efficacité de l’entrepôt, il convient de calculer ce pourcentage régulièrement, puis la moyenne sur une période plus longue. En stockage haute densité, le taux d’occupation des emplacements de stockage est considéré comme élevé lorsque le résultat est proche de 85 %.
Par exemple, si l’entrepôt est occupé à hauteur de 1 679 m3 et que sa capacité maximale est de 2 000 m3, le taux d’occupation de l’entrepôt sera de 84 %. Autrement dit, la différence résultant de l’effet nid d’abeille représenterait une perte d’espace de stockage de 16 %.
Comment atténuer le phénomène d’honeycombing warehouse ?
L’effet nid d’abeille peut entraîner un surcoût pour l’entrepôt. Bien qu’il ne puisse pas toujours être résolu, il existe des solutions logistiques qui réduisent considérablement son impact.
Une manière de réduire le nombre d’emplacements vides est la mise en œuvre d’un logiciel de gestion d’entrepôt (WMS). Ce programme de gestion permet de mettre en place une méthode d’affectation des emplacements avec stockage chaotique, c’est-à-dire qu’aucun emplacement fixe n’est réservé à une référence et elle peut donc, a priori, être stockées dans n’importe quelle alvéole disponible. De cette manière, tous les emplacements des rayonnages à palettes classiques ou des rayonnages pour picking sont utilisés. Le logiciel garantit un contrôle total du stock, tout en automatisant le stockage, en tenant compte de variables telles que la rotation des produits.
Lorsqu’il est nécessaire de compacter des marchandises très hétérogènes, les rayonnages à palettes mobiles sont une bonne solution pour éviter le phénomène de nid d’abeille. Tous les stocks sont facilement accessibles grâce à la possibilité d’ouvrir et de fermer les allées de travail. La configuration de ce système permet de ne pas perdre d’espace lors de l’application de la stratégie de stockage chaotique.
En revanche, pour le stockage de marchandises homogènes, les rayonnages drive-in représentent la solution de stockage compact la plus traditionnelle. Cependant, ce système contient la même référence dans toute l’allée (à la fois en profondeur et dans les niveaux), ce qui augmente le risque d’honeycombing. Il existe également d’autres solutions pour minimiser ce problème, comme l’installation du système Pallet Shuttle : une navette motorisée est placée dans le rayonnage compact et organise les palettes à l’intérieur des canaux. Les chariots élévateurs ne pénètrent pas à l’intérieur des rayonnages et les références peuvent être différentes à chaque niveau, ce qui augmente la capacité effective du système. Les rayonnages push-back et à palettes dynamiques permettent aussi de stocker une référence par niveau grâce aux rouleaux et à la force de gravité.
Les solutions présentées ci-dessus réduisent le phénomène d’alvéolage vertical. Cependant, il est toujours possible de générer un alvéolage horizontal (canaux à moitié vides). Pour ce faire, l’étape suivante consisterait à bien ajuster la profondeur des canaux pour réduire le risque de perte de capacité effective.

Exemple d’effet honeycombing : le cas de la SLVA
Le producteur laitier français SLVA a construit un entrepôt de 4 000 m2 ― avec seulement 2 829 m2 dédiés au stockage ― d’une capacité de plus de 7 000 palettes. Afin d’optimiser l’extraction et le stockage de ses marchandises, Mecalux a équipé l’installation du système Pallet Shuttle, qui permet le stockage de différentes références par module (une par canal).
L’entreprise a trois blocs de rayonnages compacts de différentes profondeurs en fonction du taux de rotation des produits. Pour minimiser l’honeycombing, les systèmes de stockage sont équipés d’une navette motorisée qui gère le canal et évite l’apparition d’alvéoles vides inutilisables. La division par blocs atténue l’effet nid d’abeille en stockant des produits à rotations diverses dans des rayonnages de différentes profondeurs.
Par exemple, dans l’un des blocs de rayonnage, d’une capacité de 3 792 palettes, la navette motorisée peut gérer jusqu’à 24 unités de charge en profondeur, atténuant ainsi l’alvéolage. La classification par rotation permet de stocker les produits de faible consommation dans un autre bloc de rayonnage d’une capacité, par niveau, de seulement trois palettes en profondeur.
Honeycombing warehouse : choisir la solution de stockage adaptée à chaque entrepôt
Dans un entrepôt à gestion manuelle, notamment s’il est équipé de rayonnages compacts, les flux des marchandises créent des espaces vides, temporairement inutilisables, qui constituent un obstacle à l’optimisation de la capacité effective de l’entrepôt.
Afin de limiter l’impact de l’alvéolage sur l’entrepôt, il est nécessaire de consulter un fournisseur de solutions intralogistiques de confiance qui puisse concevoir une solution basée sur les caractéristiques de l’entreprise. Avec 50 ans d’expérience, Mecalux met à votre service son expertise dans le domaine des solutions logistiques qui vous permettront de maximiser les performances de votre entrepôt. Contactez-nous, nous vous proposerons une solution pour accélérer les opérations et optimiser la capacité effective de stockage.