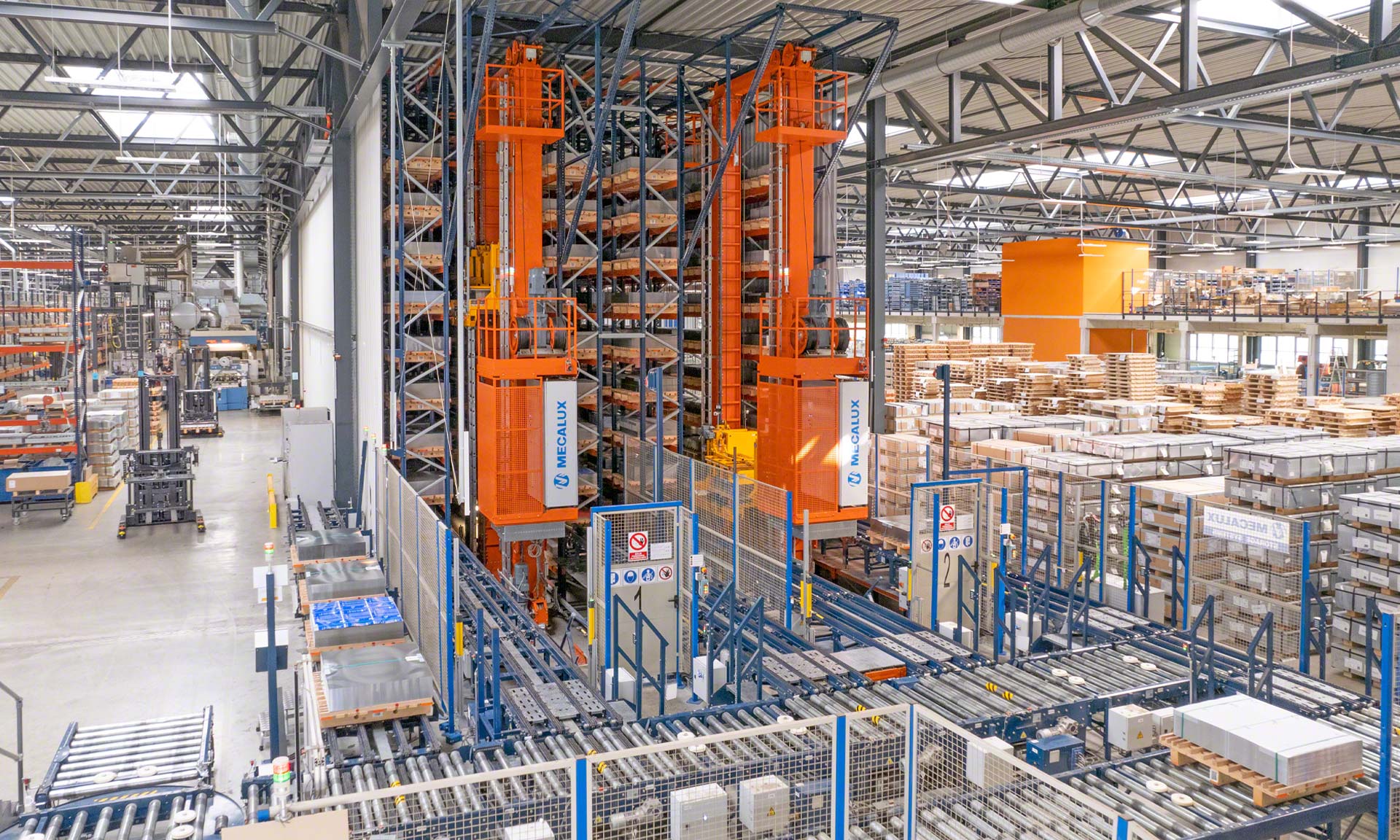
Blechwarenfabrik : l’usine de contenants métalliques la plus moderne d’Europe
Blechwarenfabrik, fabricant de contenants en aluminium à Limbourg (Allemagne), centralise tous ses processus de production et logistique dans un nouveau centre de 63 000 m² entièrement automatisé et digitalisé.
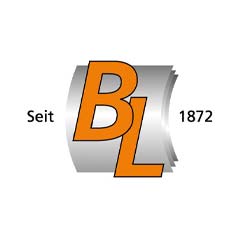
Blechwarenfabrik, fabricant de contenants en aluminium, a inauguré son nouveau siège à Offheim (Allemagne) où sont fabriqués plus de 100 millions de contenants par an. Le site comprend deux entrepôts automatisés connectés à la production par Easy WMS de Mecalux, qui supervise l'envoie des matières premières.
Blechwarenfabrik : tradition et innovation
Blechwarenfabrik est l’un des principaux fabricants européens de contenants métalliques pour de nombreux secteurs industriels (principalement pour le stockage et la manipulation de produits chimiques).
- Année de création : 1872
- Effectif : 500 personnes
- Capacité de production : plus de 100 millions de contenants métalliques par an
- Usines de production : Allemagne, Danemark, Russie et Pologne
DÉFIS
|
SOLUTIONS
|
AVANTAGES
|
---|
Blechwarenfabrik, premier producteur européen de contenants métalliques pour produits chimiques, a automatisé et digitalisé sa logistique afin de faire face à l’augmentation des ventes.
À Offheim (Allemagne), l’entreprise possède une usine de 22 000 m². Tous les flux de marchandises sont entièrement automatisés : des véhicules à guidage automatique (AGV) relient les deux entrepôts automatisés aux lignes de production en toute autonomie.
Auparavant, l’entreprise fabriquait tous ses contenants métalliques (boîtes de conserve en fer blanc pour les boissons, les aliments en boîte, etc.) dans deux sites de production en Allemagne et externalisait sa logistique en raison du manque d’espace de stockage. « La matière première était stockée dans l’entrepôt principal tandis que les produits finis, une fois sorti des lignes de production, étaient transférés vers un entrepôt situé à 5 km de là », explique Christoph Weber, responsable technique de Blechwarenfabrik.
Dans un objectif d’internalisation logistique, de réduction des coûts et de centralisation de toutes ses activités dans un unique site hautement digitalisé et durable, Blechwarenfabrik s’est lancée dans son projet le plus ambitieux à ce jour : la construction d’un nouveau siège à Offheim (Limbourg), où seront regroupées toutes ses activités. Les nouvelles installations comprennent des bureaux, 25 lignes de production et une zone de stockage. L’usine traite 22 000 tonnes d’acier destinées à la production de plus de 100 millions de contenants métalliques par an.
La centralisation de la logistique et de la production s’est déroulée par étapes, car certaines des phases de production ont dû être reconfigurées et adaptées au nouveau site. Les responsables de Blechwarenfabrik ont travaillé en étroite collaboration avec l’équipe technique de Mecalux à la conception d’une solution sur mesure. « Un projet de grande envergure comme le nôtre n’est pas facile à réaliser, car nous devions prendre en compte de nombreux détails. Avec l’aide de Mecalux, le transfert de toutes les opérations logistiques vers notre nouvelle usine s’est parfaitement réalisé », déclare M. Weber.
La robotique pour plus d’efficacité et de durabilité
S’il y a une chose sur laquelle l’entreprise était claire, c’est qu’elle voulait se lancer dans l’industrie 4.0, en choisissant la technologie pour intégrer automatiquement la production à la logistique. « Avant, la gestion des opérations et la circulation des marchandises étaient faites manuellement. La production était alimentée en marchandises à l’aide de chariots élévateurs. De plus, nos installations étaient divisées en plusieurs sites, ce qui complexifiait la logistique interne », explique le responsable technique.
Désormais, la production et le stockage sont regroupés dans la même installation et sont alimentés par quinze véhicules à guidage automatique qui déplacent les produits d’un point à l’autre de l’entrepôt, avec une intervention minimale de l’opérateur. Les robots sont pilotés par le logiciel de gestion d’entrepôt (WMS ) qui leur notifie où prendre les produits. « Nous avons automatisé la gestion des marchandises, de la réception à l’expédition des produits. En coopération avec Mecalux, nous avons construit l’usine de contenants métalliques la plus moderne d’Europe », déclare M. Weber.
La réduction de l’impact environnemental des processus de production et logistique a toujours été l’une des principales priorités de Blechwarenfabrik. En centralisant tous les processus et en supprimant ainsi le transfert de marchandises entre les usines de production et les entrepôts, l’entreprise prévoit de ne plus émettre 2 600 tonnes de gaz polluants par an.
L’usine de Blechwarenfabrik dispose également d’une zone réservée à la collecte des déchets métalliques générés par les différents processus industriels en vue de leur recyclage. 4 100 panneaux solaires ont aussi été installés sur le toit de l’usine pour générer l’énergie nécessaire aux processus de production et de stockage.
Logistique et production : une connexion efficace grâce à Easy WMS
La nouvelle usine Blechwarenfabrik comprend deux magasins automatisés : un à l’intérieur du site destiné au stockage des matières premières et un entrepôt autoportant pour les produits finis. Les entrepôts autoportants sont des bâtiments dont la structure est formée par des rayonnages sur lesquels sont fixés les panneaux latéraux et le toit. Elle a également implanté le système de gestion d’entrepôt Easy WMS de Mecalux, un logiciel qui gère et optimise tous les processus dans les deux entrepôts.
« La centralisation de la production et de la logistique a été l’un des plus grands défis de ce projet. Nous y sommes parvenus en transférant progressivement les processus de production vers les nouvelles installations. Cela nous a permis d’analyser et de résoudre les problèmes au fur et à mesure qu’ils se présentaient », explique Uwe Wonsack, directeur des opérations chez Blechwarenfabrik.
Le logiciel Easy WMS réunit efficacement la logistique et la production. Directement connecté à l'ERP Infor de Blechwarenfabrik et au système de contrôle de la production (MES), le logiciel détermine les articles nécessaires à la production et organise leur distribution. « Les programmes se complètent. Si nous recherchons des informations sur un produit, Easy WMS nous fournit tous les détails, la quantité disponible ou l’emplacement exact », explique M. Wonsack. Ensuite, l’ERP, à son tour, se connecte à d’autres logiciels impliqués dans les processus de production comme celui qui gère les robots de palettisation utilisés dans la production, celui qui collecte les données sur le développement des opérations de l’usine ou celui qui organise, contrôle et supervise ces mêmes opérations.
Easy WMS communique de même avec le logiciel de contrôle des AGV pour organiser les flux de marchandises entre les deux entrepôts et la production. « Les AGV alimentent les lignes de production de manière automatique. Lorsque Easy WMS reçoit une commande de la production, le logiciel organise sa préparation dans l’entrepôt. Les AGV prennent les produits et les transportent vers la ligne qui les a demandés. Le processus est transparent, rapide et efficace », affirme M. Wonsack.
En outre, le logiciel Mecalux organise la gestion des déchets dans l’usine de Blechwarenfabrik. Lorsque des déchets sont générés par les processus de production, Easy WMS ordonne leur envoi vers la zone de recyclage.
Logiciel de gestion d’entrepôt : une traçabilité stricte
Easy WMS de Mecalux est un logiciel qui offre une traçabilité complète des produits stockés. Le programme suit les marchandises depuis l’arrivée des matières premières jusqu’à l’expédition des produits finis. La centralisation de la logistique et de la production via Easy WMS a apporté de nombreux avantages à Blechwarenfabrik :
- Visibilité et gestion des stocks en temps réel. Easy WMS connaît le statut et l’emplacement exact des références, qu’il s’agisse de matières premières ou de produits finis.
- Soutien à la production just-in-time. Le logiciel garantit la livraison des matières premières aux processus de production dans la bonne quantité et au bon moment.
- Gestion des bases de données d'articles et des nomenclatures. Dans chaque ordre de fabrication, les matières premières nécessaires à la fabrication des produits sont configurées.
- Amélioration des processus de production. Une bonne organisation des opérations et un contrôle précis des marchandises permettent de gagner en efficacité et en souplesse.
- Travail sans papier. Les opérateurs demandent les matières premières dont ils ont besoin à partir de terminaux à radiofréquence ou via des tablettes.
« Le plus grand changement constaté avec Easy WMS a été le contrôle des stocks : nous pouvons maintenant savoir où se trouve chaque produit à tout moment », ajoute M. Wonsack. Le contrôle des stocks a permis à Blechwarenfabrik de mieux organiser les marchandises, ce qui a également un impact sur le bon déroulement des opérations. L’organisation est primordiale pour cette entreprise pour un approvisionnement just-in-time des lignes de production.
Une chaîne d’approvisionnement entièrement automatisée
Blechwarenfabrik était convaincu que l’automatisation l’aiderait à réduire ses coûts et à accroître les performances de sa chaîne d’approvisionnement. L’entreprise a optimisé et rationalisé le stockage, la préparation et l’expédition des marchandises.
Les transstockeurs, les convoyeurs pour palettes et les AGV assurent un flux permanent et contrôlé des marchandises. Chaque jour, 600 palettes de matières premières sont envoyées aux lignes de production et, dans le même temps, 1 200 palettes d’environ 500 000 boîtes de conserve et contenants métalliques sont collectées sur les lignes de production, stockées et mises à disposition pour être expédiées à des centaines de clients dans toute l’Europe.
➤ Entrepôt de matières premières
D’une hauteur de 11 m et d’une longueur de 100 m, l’entrepôt automatisé est composé de deux allées avec, de part et d’autre, des rayonnages à simple profondeur capables de stocker 2 500 palettes contenant les tôles utilisées dans la fabrication des boîtes.
L’entrepôt reçoit en moyenne 125 000 feuilles de métal par jour des fournisseurs. En liaison permanente avec le MES (Manufacturing Execution System), la première action d’Easy WMS lors de l’organisation de la réception des marchandises est de trier les feuilles pour qu’elles soient placées sur la bonne palette et dans la bonne position. En fonction de l’article à fabriquer sur les lignes de production, chaque feuille doit être placée dans une position spécifique sur la palette.
« Les marchandises sont organisées selon le critère FIFO, c’est-à-dire que la première palette entrée est la première sortie. De cette façon, nous évitons l’obsolescence de nos articles et assurons un flux continu de marchandises », explique M. Wonsack.
Pour s‘assurer que les lignes de production soient bien approvisionnées en marchandises, Easy WMS vérifie le nombre de feuilles nécessaires pour chaque commande et la position requise. En cas de quantité insuffisante, d’autres feuilles sont sélectionnées dans l’entrepôt et acheminées aux postes des opérateurs, où Easy leur indique la manière de placer les feuilles.
En suivant les instructions d’Easy WMS, les AGV prennent les feuilles à l’un des deux points de sortie de l’entrepôt automatisé et les transportent automatiquement jusqu’aux rayonnages à palettes à proximité des lignes de production.
Ces racks servent de tampon, c’est-à-dire que les matières premières y sont temporairement stockées jusqu’à ce qu’elles soient utilisées dans les lignes de production. Une fois l’emplacement vidé, il peut être réoccupé par un autre article pour le prochain ordre de production.
➤ Lignes de production
Lorsque les processus de production démarrent, Easy WMS ordonne aux AGV d’envoyer les matières premières et les produits semi-finis aux lignes de production correspondantes.
Un des produits semi-finis requis dans les ordres de fabrication sont les corps de boîte (appelés « bodies »). Ils ne sont pas stockés dans l’entrepôt automatisé, mais sont déposés directement dans des racks à palettes à côté des lignes de production. Easy WMS assure également le suivi de ces produits et ordonne leur envoi à la production en temps voulu.
En production, les opérateurs peuvent communiquer avec Easy WMS pour, par exemple, commander des palettes vides, signaler un stock défectueux ou renvoyer les matières premières en trop à l’entrepôt.
« Il est très important que les opérateurs aux lignes de production n’aient pas à réaliser de tâches secondaires et puissent se concentrer sur leur travail principal. Grâce à un terminal RF, les opérateurs peuvent être approvisionnés en produits à partir d’Easy WMS », ajoute M. Wonsack.
Suivant les ordres d’Easy WMS, les AGV ramassent en outre les déchets et les emmènent automatiquement vers la zone de recyclage.
➤ Entrepôt de produits finis
D’une capacité de 18 000 palettes, l’entrepôt automatisé autoportant a une hauteur de 31 m et comprend quatre allées avec des rayonnages à double profondeur de chaque côté.
Environ 80 palettes sont réceptionnées aux lignes de production chaque heure. Avant d’entrer dans l’entrepôt, ces produits passent par un poste d’inspection où ils sont vérifiés pour s’assurer qu’ils répondent aux exigences établies pour leur emplacement dans les rayonnages.
Ensuite, Easy WMS attribue un emplacement de stockage à chaque produit. Le logiciel intègre des règles et des algorithmes pour déterminer l’emplacement à chaque palette, en tenant compte de sa référence et de sa rotation.
En ce qui concerne les expéditions, l’ERP notifie à Easy WMS les palettes à envoyer, et affecte ensuite un quai à chaque commande sortante. Chaque heure, 100 palettes quittent cet entrepôt pour rejoindre la zone de préparation de commandes ou directement les quais. « Les processus d’expédition fonctionnent à la perfection », déclare Wonsack.
Un poste de préparation de commandes a été installé à l’avant de l’entrepôt. Là, les commandes sont préparées selon le principe du « goods to person », c’est-à-dire que les marchandises sont automatiquement acheminées aux opérateurs pour préparer chaque commande. Les boîtes sont extraites des palettes provenant de l’entrepôt puis placées sur une autre palette sur laquelle sont regroupés les articles composant la commande.
Les opérateurs disposent d’un écran et de terminaux à radiofréquence pour suivre pas à pas les instructions d’Easy WMS. Grâce à ces dispositifs, ils sont informés à tout moment des produits à retirer des palettes et des commandes dans lesquels les placer. Ainsi, Blechwarenfabrik a réduit au minimum le risque d’erreur.
D’autre part, les palettes directement envoyées à l’expédition sont étiquetées et conduites au quai correspondant. Une zone de préchargement a aussi été aménagée où les palettes sont regroupées et triées en fonction de l’ordre auquel elles appartiennent ou de l’itinéraire de transport, afin d’accélérer leur chargement.
Industrie 4.0 pour l’efficacité et la durabilité
Blechwarenfabrik a sécurisé et stimulé sa croissance grâce à la technologie. L’entreprise est passée à l’industrie 4.0 dans le but de garder un contrôle plus exhaustif de ses processus et de fournir un service plus efficace à ses clients. L’automatisation a non seulement augmenté le volume de production, puisqu’elle est en mesure de produire plus de 100 millions de contenants par an, mais elle a également apporté de la durabilité à la chaîne d’approvisionnement.
Grâce aux solutions automatisées de Mecalux et à la gestion d’Easy WMS, l’entreprise bénéficie d’une chaîne d’approvisionnement interconnectée. Tous les processus sont coordonnés par le logiciel dans un seul but : approvisionner les lignes de production au bon moment. La combinaison de la digitalisation et de l’automatisation est synonyme de réussite pour Blechwarenfabrik et contribuera sans aucun doute au développement futur de l’entreprise.
Lorsque nous avons ouvert notre nouvelle usine à Offheim (Limbourg), nous étions convaincus que nous devions passer à l’automatisation. La technologie fournie par notre partenaire Mecalux a considérablement modernisé notre chaîne d’approvisionnement.
Galerie
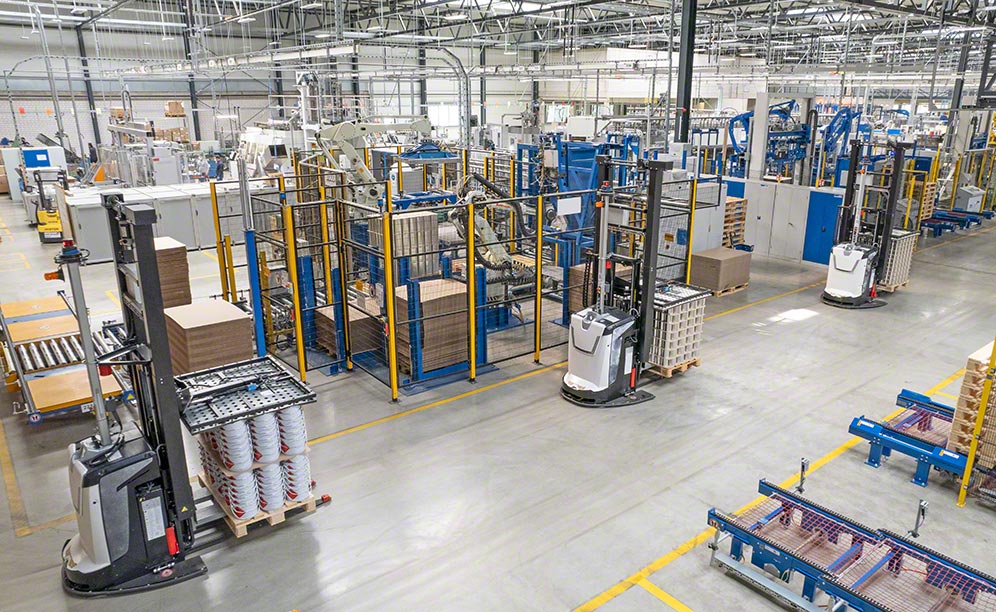
Magasin automatique de matières premières de Blechwarenfabrik à Limburg (Allemagne)
Demandez conseil à un expert