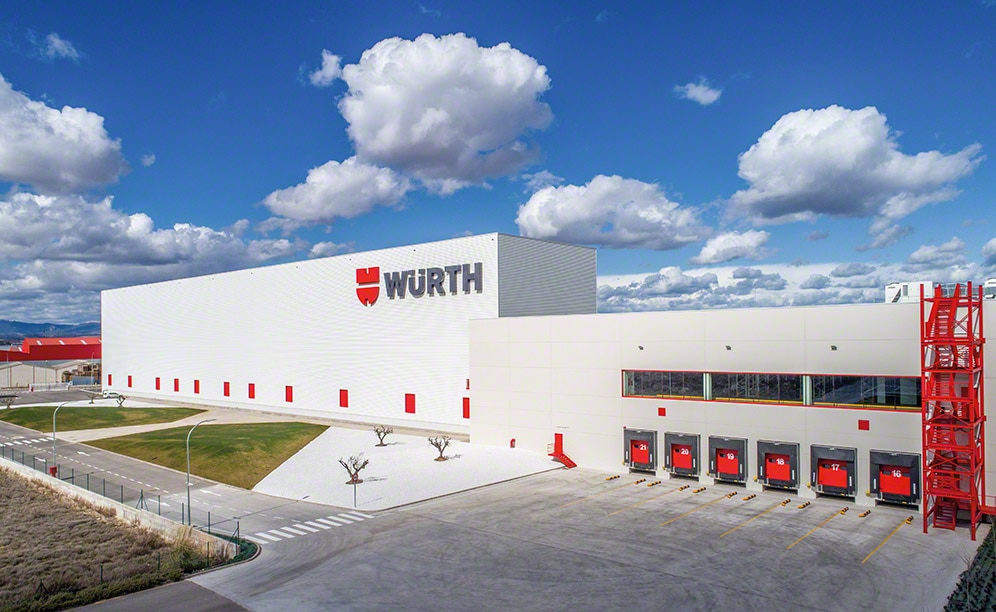
Un entrepôt clé en main 100 % automatisé pour Würth à La Rioja
Würth stocke tout son catalogue d'outils, de vis, de chevilles et de forets dans un nouveau centre de La Rioja
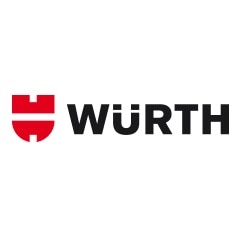
À l’occasion du 40e anniversaire de l’arrivée de Würth en Espagne, la multinationale a agrandi ses installations situées à Agoncillo (La Rioja) avec des solutions développées, fabriquées et installées par Mecalux. L’entreprise a récemment inauguré un nouveau bâtiment de réceptions et expéditions, ainsi qu’un entrepôt autoportant de palettes, entièrement automatisé. Cet entrepôt possède une capacité de stockage de 15 190 palettes, et peut déplacer jusqu’à 300 palettes en une heure ! Würth peut ainsi garantir un service de haute qualité à ses clients pour la livraison des commandes sur tout le territoire espagnol.
Würth : plus de 40 ans en Espagne
Würth est une entreprise allemande qui commercialise tout type d’éléments de fixation, d’union et de montage pour les professionnels de secteurs tels que la construction, l’automobile, la chimie, la plomberie, etc. Son large choix de produits, composé de plus de 125 000 références, inclut des vis, des chevilles, des outils de forage et de coupe, des outils, des vêtements de travail, etc. L’entreprise a été créée en 1945, dans le petit village de Künzelsau (dans le centre de l’Allemagne), comme grossiste en vis. Aujourd’hui, elle y maintient son siège et dispose désormais d’environ 74 000 employés dans plus de 80 pays répartis sur les cinq continents.
C’est en 1977, que Würth arrive en Espagne avec pour objectif celui de satisfaire les besoins des 250 000 clients de ce pays. Elle installe son siège et un premier centre logistique à Palau-solità i Plegamans (Barcelone), puis un second à Agoncillo (La Rioja). La division espagnole devient l’une des plus grandes entreprises du groupe Würth, après la centrale d’Allemagne. Aussi, ces dernières années, afin de renforcer cette croissance, elle a agrandi et modernisé son centre logistique de La Rioja. À côté de l’entrepôt construit initialement, elle a envisagé la construction d’un entrepôt automatisé autoportant, d’un bâtiment pour les quais de chargement, ainsi que de places de parking pour ses employés et les visiteurs.
Lors de la conception de cet agrandissement, Würth a exigé que les opérations effectuées dans son centre logistique ne soient pas perturbées par les travaux. Selon Pedro Montenegro, directeur logistique de Würth Espagne, « nous avons travaillé main dans la main avec les ingénieurs et les directeurs du projet de Mecalux pour que le chantier n’ait aucune répercussion sur nos clients. »
Cet entrepôt répond largement aux exigences de l’entreprise, ainsi qu’à ses perspectives de croissance pour lesquelles un espace a été réservé pour un prochain agrandissement. La technologie a été l’un des moteurs de la croissance de Würth. Aussi le centre logistique dispose également des engins les plus modernes pour effectuer les tâches de stockage et les déplacements de la marchandise vers les autres zones de manière automatique, avec une intervention minimale des opérateurs.
Mecalux a conçu des convoyeurs, des transstockeurs, des élévateurs et des monorails électriques, qui ont pour mission de garantir les flux désirés par l’entreprise pour approvisionner les clients dans les plus brefs délais. Attentif aux détails, Mecalux a aussi adapté les couleurs de l’entreprise Würth aux différents éléments fournis : les rayonnages, les transstockeurs, les monorails électriques, les élévateurs et les convoyeurs sont de couleur rouge et blanche.
Pedro Montenegro - Directeur logistique de Würth Espagne
« Un partenaire était essentiel pour nous. Trouver une entreprise qui nous ressemble, avec laquelle nous pensions pouvoir construire de grands projets sur le long terme. Mecalux a rempli les conditions nécessaires pour être ce partenaire idéal pour tous ces agrandissements logistiques. »
Entrepôt autoportant : les rayonnages soutiennent le bâtiment
L’entrepôt automatisé autoportant se distingue par ses importantes dimensions des autres bâtiments : il mesure 26 m de haut, 115 m de long et 23 m de large.
Travailler avec des dizaines de milliers de références représentait un véritable défi pour l’entreprise. Il était donc indispensable d’exploiter la surface disponible pour offrir la capacité de stockage la plus grande possible. Selon Pedro Montenegro, « l’un des grands avantages que nous a apporté la solution installée par Mecalux a été que, sur une superficie de seulement 3 500 m2, nous pouvons stocker jusqu’à 15 000 palettes. L’entrepôt de rayonnages à palettes que nous avions auparavant ne nous permettait pas d’obtenir de telles performances. »
L’entrepôt se compose de cinq allées avec des rayonnages à simple profondeur de chaque côté, dotés de leurs transstockeurs correspondants pour les mouvements d’entrée et de sortie de la marchandise. Ces machines travaillent à une vitesse de translation de 220 m/min et 54 m/min en levage, et peuvent déplacer jusqu’à 300 palettes par heure en cycles combinés, c’est-à-dire, en effectuant les entrées et les sorties de manière simultanée.
Tout le système est contrôlé par le logiciel de gestion d’entrepôt Easy WMS de Mecalux, qui communique avec le système informatique de Würth pour réaliser le suivi et la gestion de la marchandise tout au long de son entrée, de sa sortie et de son stockage.
Un bâtiment adossé à l’entrepôt
Un bâtiment de 15 m de haut, divisé en deux étages destinés à des opérations différentes, a été érigé entre le nouvel entrepôt automatisé et l’entrepôt construit précédemment.
Étage inférieur
Au niveau inférieur, sont effectuées les entrées ainsi que les sorties des produits sur douze quais de chargement et déchargement. Pour ce faire, un circuit de convoyeurs avec trois postes d’entrée et deux de sortie a été installé. Les palettes constituées d’une unique référence ayant été reçues sont vérifiées à cet étage. Celles comportant plus d’une référence seront déposées provisoirement dans les rayonnages, en attendant d’être vérifiées à l’étage supérieur. Afin d’être stockées, ces palettes doivent traverser un poste d’inspection d’entrées (PIE) où sont révisés le poids, les dimensions des charges (gabarit), l’état des palettes (alvéoles, chevilles et patins), et où est identifié le produit au moyen de la lecture de l’étiquette contenant le code-barres.
L’une des lignes d’entrée dispose d’un système automatique qui fournit des palettes esclaves, dans le cas où les palettes ne seraient pas en bon état. Une fois que la marchandise a passé le contrôle, un élévateur la monte jusqu’à l’étage supérieur pour qu’elle entre dans l’entrepôt automatisé. Cet élévateur descend également les palettes provenant de l’entrepôt automatisé jusqu’à la zone des expéditions.
Les palettes esclaves qui seront utilisées à nouveau dans les entrées sont récupérées et empilées au bout de la ligne de sortie. Celles qui sont expédiées sont regroupées dans la zone de préchargements au sol, juste en face des quais, en fonction de si elles correspondent à une même commande ou à un même itinéraire de transport.
L’installation comprend deux élévateurs. L’un monte les palettes de la zone de réception jusqu’à l’étage supérieur (entrées) et les descend de l’étage supérieur jusqu’à la zone des expéditions (sorties). L’autre descend les palettes provenant de l’entrepôt automatisé jusqu’au premier étage de l’entrepôt existant.
Étage supérieur
À l’étage supérieur, un circuit monorail électrique transporte les palettes qui vont entrer dans l’entrepôt automatisé jusqu’à l’allée qui leur a été assignée par le logiciel Easy WMS de Mecalux. En même temps, les palettes qui se dirigent vers les expéditions sont récupérées et transportées jusqu’à l’élévateur, qui les descend jusqu’à l’étage inférieur.
C’est également à cet étage que les palettes formées par plusieurs références et qui avaient été stockées temporairement sont vérifiées. C’est ici que les références sont séparées et classées, que les quantités sont vérifiées et que les produits sont identifiés et à nouveau envoyés vers l’entrepôt automatisé.
Deux postes de picking ont été aménagés devant le circuit monorail électrique. C’est là que sont préparées les commandes de caisses complètes des produits qui sont stockées dans l’entrepôt automatisé. Accélérer au maximum cette opération était une priorité pour Würth. L’installation a donc été conçue pour fournir un maximum de 60 palettes par heure à chaque poste de picking.
Les postes de picking disposent des équipements nécessaires pour effectuer les différentes tâches, comme des ordinateurs, des imprimantes d’étiquettes et des bras pneumatiques, qui facilitent la manutention des produits (qui peuvent être volumineux et très lourds). À l’aide des manipulateurs industriels, les opérateurs récupèrent les articles directement des palettes que les monorails électriques ont approchées des postes de picking et les déposent sur une autre palette. Les produits qui composent chaque commande sont regroupés sur cette dernière palette. Un maximum de huit commandes peuvent être préparées simultanément à ces deux postes.
À l’étage supérieur, se trouve aussi un circuit de convoyeurs qui relie le nouvel entrepôt automatisé à l’entrepôt que Würth avait déjà construit. Cet entrepôt d’une capacité de stockage d’environ 10 000 palettes, est destiné à des produits qui, en raison de leurs dimensions et de leur type (chimiques), ne peuvent pas être stockés dans l’entrepôt automatisé. Le picking d’unités de toutes les références y est en outre effectué. Les convoyeurs sont chargés d’approvisionner l’entrepôt avec les produits nécessaires pour pouvoir effectuer le picking.
Les avantages pour Würth
- Solution sur mesure : réutilisation de la surface qui offre une capacité de stockage pour 15 190 palettes et un espace réservé pour un possible futur agrandissement.
- Entrepôt hautement technologique : le nouvel entrepôt est entièrement automatisé, ce qui garantit un flux élevé de mouvements fluides et sans erreurs.
- Priorité à la préparation de commandes : l’entrepôt automatisé comprend une zone spécifique où effectuer le picking de caisses complètes et un circuit de convoyeurs approvisionne l’entrepôt déjà construit avec la marchandise nécessaire pour réaliser le picking de petites unités.
Entrepôt autoportant | |
---|---|
Capacité de stockage: | 15 190 palettes |
Dimensions des palettes: | 800 x 1 200 mm |
Poids max. des palettes: | 1 000 kg |
Hauteur de l’entrepôt: | 26 m |
Longueur de l’entrepôt: | 115 m |
Largeur de l’entrepôt: | 23 m |
Galerie

L’entreprise allemande a inauguré un nouvel entrepôt à La Rioja (Espagne)
Demandez conseil à un expert