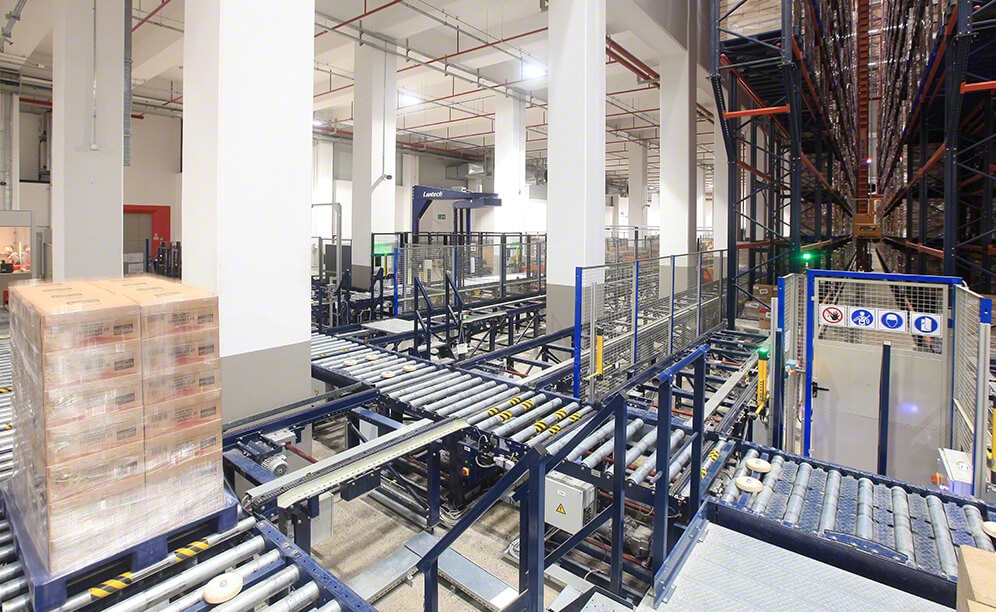
L'entrepôt automatisé de noix et fruits secs de Tadım en Turquie
L'entrepôt automatisé de Tadım en Turquie gère 5 300 palettes de produits finis
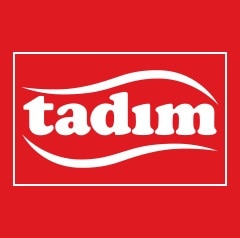
Tadım, distributeur de noix et d’autres fruits secs, a inauguré un entrepôt automatisé dans la ville de Gebze (Turquie). Dans ces installations, elle stocke plus de 5 300 palettes de produits finis, prêts à être distribués à ses clients. L'intégration de la technologie de pointe dans tous ses processus logistiques, y compris le logiciel Easy WMS de Mecalux, fait partie de sa stratégie visant à pénétrer progressivement l’industrie 4.0. En conséquence, elle a augmenté sa capacité de stockage de 143 %, amélioré sa productivité et renforcé son processus d'expansion internationale.
Entreprise leader en Turquie
Fondée à Gaziantep, en Turquie, Tadım est une entreprise pionnière dans l'élaboration et l'emballage de noix et d’autres fruits secs. Dès le lancement de son activité en 1971, l’entreprise s’impose des normes très strictes afin de garantir la meilleure qualité des produits. Selon Kemal Güler, responsable logistique chez Tadım, « l’entreprise possède une image de marque très solide, une équipe de collaborateurs passionnés et une direction tournée vers l'avenir. Toutes ces synergies se sont matérialisées dans une augmentation de la part de marché de Tadım en Turquie au fil des ans, et dans son internationalisation ».
À l’heure actuelle, elle dispose de quatre centres de production en Turquie et en Allemagne, en plus d'un réseau de commercialisation qui couvre l’Europe et les États-Unis.
Les installations de Tadım
Tadım possède à Gebze, au sud-ouest d'Istanbul, l’un de ses plus grands centres de production en Turquie. Il occupe une surface totale de 25 000 m2 et y concentre toute la gamme de produits (y compris ceux en provenance d’autres usines) nécessaires pour effectuer des procédés dont le salage, le grillage, l'emballage et le conditionnement. Jusqu’ici, Tadım disposait d'un entrepôt capable de stocker 2 000 palettes, une capacité insuffisante pour son activité. « Nous avions besoin d’une plus grande capacité »souligne M. Kemal Güler. « La gamme de produits, comme le territoire de distribution de Tadım, s'agrandissaient très rapidement. Nous avions donc besoin de plus d'espace de stockage et nous étions obligés d’accélérer les entrées et les sorties ».
L'entreprise envisageait de construire un nouvel entrepôt en réservant l'espace occupé par l’ancien à la mise en place d'avantage de lignes de production. Pour cela, elle a contacté Mecalux. « Nous avons fait appel à Mecalux, car elle est un leader incontesté dans le secteur des solutions de stockage à échelle mondiale. La principale raison de notre choix a été notre étroite relation avec l’équipe technique de Mecalux en Turquie », indique le responsable logistique.
L’équipe technique de Mecalux en Turquie s'est déplacée à Gebze afin de visiter les installations de Tadım et de réaliser une analyse approfondie des besoins et spécificités de l'entreprise. « Nous avons créé une équipe de projet pour trouver la solution qui s’adapte au mieux à nos exigences. De son côté, Mecalux nous a présenté deux solutions : un entrepôt automatisé et un système de gestion d’entrepôt. Les deux étant complémentaires et leur mise en place réalisable pour nous », explique Kemal Güler.
L'installation d’un entrepôt automatisé était une décision très importante pour Tadım, parce qu'elle impactait directement ses performances. C’est pourquoi, les responsables de l'entreprise souhaitaient être complètement sûrs de toutes les options possibles avant de prendre leur décision finale.
Selon Kemal Güler,« l’équipe Mecalux nous a organisé un voyage en Espagne et nous a invités à visiter un autre entrepôt où des opérations très semblables aux nôtres sont réalisées. Dans cet entrepôt, nous avons pu voir ces solutions présentées sur papier et nous avons été convaincus que Mecalux était le meilleur prestataire pour nous ».
Caractéristiques de l'entrepôt automatisé
Il occupe une surface de 7 700 m2 et est composé de trois allées de 70 m de long, dotées de rayonnages à simple profondeur de chaque côté. « Pour l'instant, nous disposons de trois allées, mais un espace a été réservé pour trois allées supplémentaires lorsque nous en aurons réellement besoin » , précise le responsable logistique de Tadım.
Les rayonnages mesurent 23 m de haut, répartis sur treize niveaux, et offrent une capacité de stockage totale de 5 364 palettes avec environ 120 références. « Cet entrepôt nous a permis d'augmenter de 143 % la capacité de stockage par rapport à notre ancienne installation », se réjouit Kemal Güler.
Dans chaque allée, un transstockeur est chargé de récupérer les palettes des convoyeurs d'entrée et de les déposer à l'emplacement qui leur a été assigné par Easy WMS, le logiciel de gestion d’entrepôt de Mecalux. La manipulation automatisée des charges a eu un impact direct sur la productivité de l’entrepôt et sur la satisfaction des clients : « Nous avons diminué de 85 % le nombre de palettes endommagées », assure le responsable logistique.
Les transstockeurs se déplacent à une vitesse de 220 m/min en translation et 66 m/min au levage, ce qui permet de compléter 100 cycles combinés par heure (100 palettes d’entrée et 100 de sortie).
L'entrepôt est situé à proximité du centre de production. « Les deux sont reliés entre eux par un circuit de convoyeurs », déclare Kemal Güler. Ce circuit a pour fonction de transporter les palettes provenant de la production jusqu’à l’entrée de l'entrepôt et, en même temps, de transporter les palettes vides et les retours de l'entrepôt jusqu’à la production.
L’automatisation des entrées a signifié un bond en avant pour Tadım. Selon Kemal Güler, « nous avons augmenté de 73 % le nombre de réceptions quotidiennes ». . En moyenne, 1 000 palettes sont reçues par jour, de sorte que ce système de transport garantit un flux continu de marchandise et minimise l'activité des engins de manutention (en réduisant aussi le risque d’accidents).
Kemal Güler - Responsable logistique de Tadım
« Le nouvel entrepôt a répondu à tous les besoins que nous avons présentés à l’équipe technique de Mecalux. Nous avons augmenté la capacité de stockage (nous l'avons doublée) et, en même temps, nous avons augmenté le nombre d’entrées et de sorties quotidiennes grâce à l'amélioration de la productivité. De même, l'efficacité du système de gestion d’entrepôt au cours des derniers mois a été de 99,1 %. Nous sommes en mesure d'affirmer que nous disposons d'un système dans lequel nous pouvons avoir confiance. »
Les avantages de l’automatisation de l'entrepôt
« À l'ère de l'industrie 4.0, le numérique est un axe central dans notre vision de futur »affirme le responsable logistique de Tadım. L'industrie 4.0 consiste à mettre en place les technologies numériques dans l’ensemble des processus de production et logistiques afin de les rendre plus performants.
Le numérique a de nombreux avantages pour les entreprises, parce qu'il leur permet de s’adapter facilement aux changements de la demande et aux nouvelles habitudes de consommation, ainsi que d’offrir aux clients un service personnalisé ou encore, de réduire le temps nécessaire pour concevoir, produire et commercialiser les produits. Tadım cherchait à améliorer les performances de son nouvel entrepôt. Pour cela, « l'automatisation était la meilleure solution pour nous, en comparaison aux les systèmes de stockage traditionnels », ajoute Kemal Güler.
Dans les entrepôts automatisés les engins électromécaniques (convoyeurs, transstockeurs, navettes…) effectuent les opérations qui, dans un entrepôt non automatisé, sont attribuées aux opérateurs qui les réalisent à l’aide de chariots traditionnels (notamment les transferts de marchandise et l’emplacement de celle-ci dans les rayonnages).
L’automatisation de l’entrepôt a plusieurs avantages pour les entreprises :
- Une exploitation maximale de l'espace et du volume de construction
- Un contrôle total de la marchandise stockée et une optimisation de la capacité de stockage.
- Un inventaire permanent.
- Une amélioration des performances opérationnelles et une disponibilité accrue.
- Une diminution des coûts de maintenance structuraux.
- Une réduction des coûts d'exploitation.
- Une marchandise en sécurité et un risque d'accidents plus faible.
- Un fonctionnement 24 heures sur 24, sans interruption.
- Menor coste de personal.
Zone de préparation des commandes et d’expédition
Environ 40 commandes de 24 lignes chacune en moyenne sont préparées par jour. Une zone spécifique a été aménagée pour mener à bien cette opération, juste à côté de l’entrepôt automatisé.
57 canaux dynamiques (chacun correspond à une référence) ont été installés, mais un espace est réservé pour de futurs canaux supplémentaires.
Ces canaux, appuyés au sol, sont légèrement inclinés pour que les palettes se déplacent sous l'effet de la gravité de la partie la plus élevée jusqu’à la partie la plus basse. Les opérateurs accèdent directement aux palettes par la partie la plus basse et prélèvent les caisses qui composent chaque commande.
Les canaux sont disposés parallèlement, avec une allée centrale où circule une navette qui distribue les palettes dans les canaux correspondants. Chaque canal peut contenir jusqu’à deux palettes maximum de la même référence, ce qui permet d’avoir un stock de marchandise à tout moment.
Une fois toutes les commandes préparées, elles sont stockées en attendant d’être transférées à la zone d’expédition, située juste en face des allées de stockage. Cette zone est composée de 21 canaux dynamiques de préchargement d'une profondeur maximale de 16 palettes. Une navette trie la marchandise dans ces canaux de préchargement. Les palettes sont regroupées dans chaque canal en tenant compte leur appartenance à la même commande ou le même itinéraire ; elles sont ainsi préparées jusqu'à leur chargement ultérieur dans les camions.
« Grâce à la conception et l'organisation de la zone d'expédition, nous avons augmenté de 56 % le nombre de palettes qui quittent l'entrepôt », , indique Kemal Güler. 1 000 palettes sont distribuées quotidiennement, dont 95 % sont livrées à des supermarchés et des petites boutiques en Turquie. Le 5 % restant sont principalement livrées aux clients de Tadım situés dans la péninsule des Balkans (à destination de la Roumanie, le Kosovo, l'Albanie, etc.).
Un système informatisé pour un projet de grande envergure
Pour une installation d'une telle envergure et dotée d'un processus opérationnel entièrement automatisé comme celle de Tadım, il est indispensable de mettre en place un système de gestion d’entrepôt (WMS) efficace et conçu pour effectuer le suivi de tous les processus de l'installation : entrée de la marchandise, stockage, préparation des commandes et expéditions. De même, afin d'obtenir une gestion globale de l'entrepôt, le logiciel Easy WMS doit communiquer en permanence et de manière bidirectionnelle avec l'ERP SAP de Tadım. Les deux systèmes partagent des informations comme les produits qui sont sur le point d'arriver à l'entrepôt ou encore les commandes passées par les clients et que, par conséquent, il faut préparer et distribuer rapidement.
Avant d'entrer dans l'entrepôt, les palettes provenant de la zone de production doivent traverser un poste d'inspection d’entrées (PIE) où le poids, les dimensions des charges (gabarit), l’état des palettes (alvéoles, dés et patins) sont contrôlés, et où le produit est identifié via lecture du code-barres. Les opérateurs vérifient également à ce moment-là que les palettes reçues correspondent à celles qui devaient arriver selon la notification préalable de l'ERP SAP de Tadım. Les palettes stockées quotidiennement dans les rayonnages peuvent contenir des produits finis provenant des lignes de production, des commandes préparées dans la zone de picking, ou encore des retours des clients. Un contrôle rigoureux des produits évite tout risque d'erreur et augmente la performance de toutes les opérations.
Easy WMS doit connaître les caractéristiques des produits qui entrent dans l'entrepôt. La rotation de la marchandise est l’une des principales contraintes pour assigner un emplacement dans les rayonnages. Ainsi, les produits à rotation type A, par exemple, sont déposés aux extrémités des rayonnages, près des convoyeurs, parce que leurs entrées et sorties sont plus fréquentes. Les produits à rotation type C, en revanche, sont placés à la fin de l’allée. Il faut également prendre en compte la date de production ou la date de péremption de chaque article.
La préparation des commandes est une opération clé pour Tadım. Pour cette raison, la bonne conception de la zone de picking ainsi que les directives du logiciel Easy WMS permettent à l'entreprise de préparer un grand volume de commandes par jour. Le WMS se charge d’approvisionner les canaux dynamiques de picking au besoin, afin que les articles requis soient en stock à tout moment et pour éviter les attentes des opérateurs pour préparer chaque commande. Le réapprovisionnement se fait automatiquement, le système utilise des convoyeurs et des navettes pour déplacer les palettes de l'entrepôt automatisé jusqu’aux emplacements spécifiques dans les canaux dynamiques.
Lors du picking, il faut également tenir compte des caractéristiques des produits qui composent chaque commande et vérifier s'ils sont empilables. Un itinéraire à suivre par les opérateurs lorsqu’ils préparent une commande a été conçu. Il consiste à prélever dans un premier temps les produits les plus lourds, puis les plus légers. Les opérateurs disposent de terminaux de radiofréquence pour communiquer avec Easy WMS. Le système leur indique les références à prélever directement des palettes situées sur les canaux dynamiques. Une fois le prélèvement fait, l’opérateur confirme l’action.
Lorsque les commandes sont terminées, elles sont stockées en attendant d'être transférées jusqu’à la zone d’expédition. Easy WMS organise les palettes au fur et à mesure qu'elles sortent de l'entrepôt suivant une séquence déterminée. Les palettes sont classées dans chaque canal en fonction de la commande ou de l'itinéraire. De plus, elles sont organisées en fonction du moment où elles seront livrées. Ainsi, les palettes qui sont livrées en premier, par exemple, doivent quitter l'entrepôt en dernier pour être placées à la fin du canal de préchargement et, par conséquent, du camion.
Les avantages pour Tadım
- Un fonctionnement automatisé : Tadım bénéficie d'un fonctionnement et d'une gestion de la marchandise entièrement automatisés qui lui ont permis d'éliminer tout risque d'erreur et d'augmenter la productivité.
- Une préparation de commandes efficace : une zone de picking est destinée à cette tâche afin de préparer autant de commandes que possible (jusqu'à 40 par jour avec 24 lignes chacune).
- Une plus grande capacité de stockage : l'entrepôt offre une capacité de stockage de 5 634 palettes, soit 143 % de plus par rapport à l'ancien entrepôt de Tadım.
Entrepôt automatisé de Tadım | |
---|---|
Capacité de stockage: | 5 364 palettes |
Dimensions des palettes: | 800 x 1 200 mm |
Poids max. des palettes: | 200 kg |
Hauteur de l'entrepôt: | 23 m |
Longueur de l'entrepôt: | 70 m |
Galerie
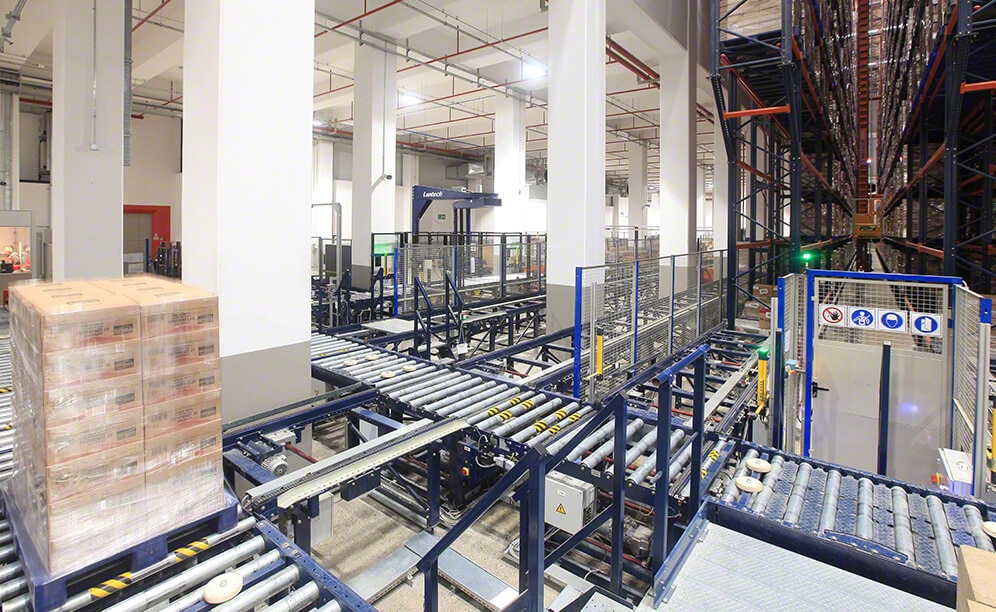
Demandez conseil à un expert