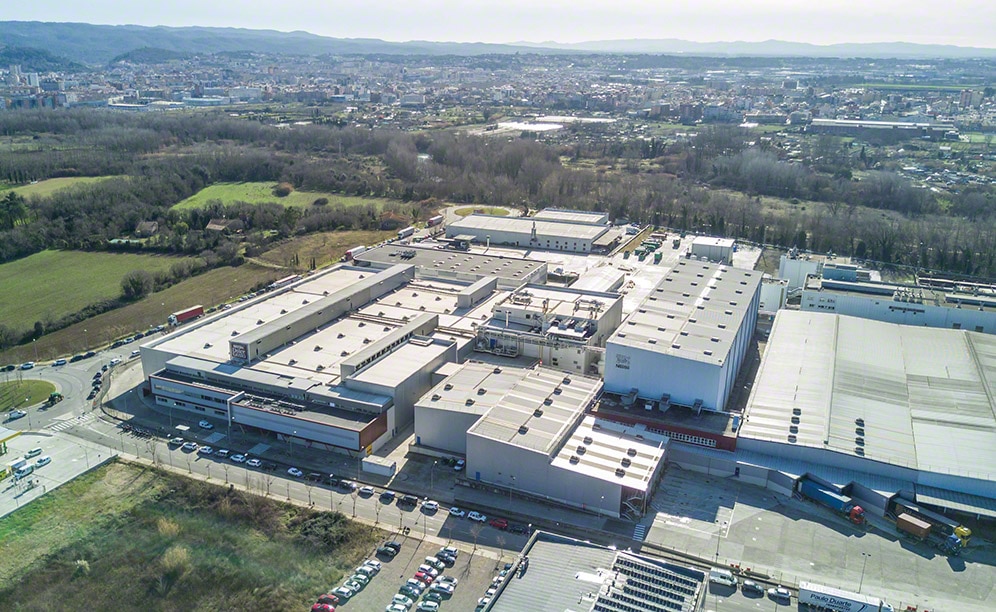
Un circuit de convoyeurs Mecalux dans le centre de production de Nestlé
Les convoyeurs comme les élévateurs accélèrent rapidement le déplacement de la marchandise
L'usine de Nescafé située à Gérone en Espagne, est l’un des centres de production les plus compétitifs de Nestlé. C'est un projet ambitieux, qui s’adapte constamment aux nouveaux besoins du marché. Depuis 1990, Mecalux accompagne Nestlé dans ce centre, en concevant et en appliquant les solutions les plus performantes pour améliorer sa logistique et renforcer ses perspectives d'avenir.
Sobre Nestlé y Nescafé
Nestlé est un des principaux acteurs mondial de l’industrie agroalimentaire, avec une présence dans plus de 191 pays. Elle dispose de près de 2 000 marques, qui offrent une grande variété de produits : aliments pour bébés, eau en bouteille, céréales pour le petit-déjeuner, café et thé, confiserie, produits laitiers, aliments pour animaux de compagnie ou produits apéritifs, entre autres.
Actuellement, elle possède dix centres de production en Espagne, répartis dans cinq régions. Ces usines sont spectaculaires de par leur haute performance et exportent 44 % de leur production vers d'autres pays.
En 1968, Nestlé a construit un centre de production à Gérone destiné à la fabrication de café soluble Nescafé et, depuis 2009, des capsules de Nescafé Dolce Gusto. Le site a connu une forte croissance au cours de ces dernières années, jusqu'à devenir la plus grande usine de production de café soluble de la multinationale.
Nescafé est la marque de café instantané appartenant à Nestlé. Elle a été lancée en 1938 et, depuis, a agrandi son catalogue en introduisant des recettes et des saveurs nouvelles et innovantes pour satisfaire chaque goût, chaque occasion ou chaque budget.
Mecalux et Nestlé
La collaboration entre les deux entreprises a commencé en 1990, lorsque Mecalux a construit un magasin automatisé autoportant pour palettes dans l'usine de Nescafé située à Gérone.
Cet entrepôt, de 25 m de haut et de 107 m de long, est composé de sept allées traversées par des rayonnages à simple profondeur, de part et d'autre, qui offrent une capacité de stockage de 16 380 palettes. Y sont stockés les produits finis, prêts à être envoyés aux expéditions.
Quelques années plus tard, en 2006, Mecalux a construit un second entrepôt autoportant de 21 m de haut, à quelques mètres de distance du premier entrepôt. Il est formé de deux allées dotées de rayonnages à simple profondeur où sont déposés un total de 740 conteneurs de matières premières.
L’entrepôt est adapté aux mesures et caractéristiques des conteneurs de Nestlé : ils mesurent 1 210 x 1 060 x 1 810 mm et ne sont pas équipés de patins inférieurs. L’entrée et la sortie sont réalisées à l’aide de convoyeurs qui déplacent la marchandise jusqu'à l'extrémité des deux allées de stockage. Pour faciliter leur transfert sur les convoyeurs, les conteneurs sont placés au-dessus d’une palette esclave.
De même, les niveaux des rayonnages sont équipés de supports qui permettent que les conteneurs s’appuient dessus sans avoir recours à la palette esclave.
Nescafé Dolce Gusto
Nestlé a commencé à commercialiser les capsules de thé et de café Nescafé Dolce Gusto en 2005. Le centre de production était situé initialement au Royaume-Uni mais, au vu du volume de vente du produit en Espagne, l’entreprise a décidé d'installer une nouvelle usine dans ce pays afin d'approvisionner son marché plus rapidement..
L’entreprise a agrandi le centre de production de Gérone en 2009 et a construit l'usine de Nescafé Dolce Gusto à côté des installations existantes. Avec l’accompagnement de Mecalux, ce centre s’est agrandi et adapté, au cours de différentes étapes, aux nouvelles exigences de Nestlé :
Première intervention
La société a sollicité Mecalux dans le but de relier la nouvelle usine de Nescafé Dolce Gusto à l’entrepôt de produits finis. Elle avait besoin d'un système de transport rapide qui lui fournirait un flux de mouvements constant entre deux points. Le projet représentait un véritable défi, étant donné qu'il fallait relier deux entrepôts séparés l'un de l'autre par une rue. Mecalux a proposé la construction d’un pont surélevé et couvert – à 6 m de haut au-dessus du sol – qui relierait les deux bâtiments entre eux, avec un circuit de convoyeurs situé à l’intérieur.
Cette solution évite les interférences avec la circulation habituelle. Les produits sont, quant à eux, protégés contre les intempéries. Les convoyeurs à rouleaux se déplacent à une vitesse de 20 m/min. Leur fonctionnement est entièrement automatisé et requiert une intervention minimale de la part des opérateurs ; supprimant ainsi les erreurs provenant de la gestion manuelle.
Deuxième intervention
En 2011, Nestlé a installé deux élévateurs supplémentaires qui relient les deux étages du centre de production entre eux.
Un circuit de convoyeurs déplace la marchandise directement vers les élévateurs. Les convoyeurs se trouvent à une hauteur plus élevée, soutenus par une structure résistante, qui garantit leur stabilité.
Cela a permis d'exploiter la surface du centre de production, ainsi que d'éviter les interférences avec les autres opérations.
Troisième intervention
Face à l'augmentation des ventes de Nescafé Dolce Gusto, en 2012, l’entreprise avait besoin d'augmenter le nombre de mouvements de palettes entre le centre de production et l’entrepôt de produits finis.
Pour cela, Mecalux a installé un nouvel élévateur à la sortie de production permettant de doubler la quantité initiale de palettes déplacées.
Quatrième intervention
Nestlé souhaitait relier le centre de production à l’entrepôt des expéditions, pour y envoyer directement la marchandise, sans entrer dans l'entrepôt.
Mecalux a installé une nouvelle sortie dans le circuit de convoyeurs , qui quitte le centre de production. La marchandise traverse le pont surélevé et, avant d'atteindre l'entrepôt, un élévateur descend les palettes correspondantes jusqu'aux expéditions.
La société avait besoin d'automatiser la zone des expéditions, pour optimiser ainsi la productivité de toutes les opérations:
- Zone de remontage. Une navette distribue les palettes entre six convoyeurs, où elles attendent pour rejoindre la machine automatique de remontage qui empile une palette au-dessus de l’autre.
- Canaux de préchargement. Une autre navette saisit les palettes empilées et les répartit entre six canaux de préchargement, formés par des convoyeurs à rouleaux légèrement inclinés. Ce système regroupe les palettes d’une même commande ou d'un même itinéraire.
- Zone de préchargement au sol. Une zone de préchargement au sol a été aménagée juste en face des canaux dynamiques. Les commandes sont préparées avant le chargement du camion de transport et de distribution, afin d’éviter les temps d’attente lorsque la marchandise sort de l’entrepôt.
Cinquième intervention
À côté de l’entrepôt des expéditions, se trouve l'entrepôt de big-bags ou sacs industriels contenant des matières premières. Ces sacs sont placés sur des palettes pour faciliter leur déplacement et stockage dans les rayonnages.
L’entrée de l’entrepôt s'effectue automatiquement, par le biais d'un circuit de convoyeurs. Les palettes passent par un poste de contrôle pour vérifier que leur état, leurs poids et dimensions respectent les critères de qualité requis.
Ensuite, un élévateur transporte la marchandise jusqu'à l’étage supérieur, où se trouvent deux blocs de rayonnages à palettes par accumulation drive-in.
Les rayonnages se composent d’un ensemble d'allées de 6,5 m de haut, chacune ayant trois niveaux. Chaque niveau dispose de rails de guidage fabriqués en tôle d’acier galvanisé à résistance élevée où sont déposées les palettes avec les sacs par-dessus.
Logiciel de commande
Face à l'envergure de ce centre de production, il est important d'utiliser un système informatisé qui contrôle et dirige tous les mouvements des engins de manutention automatiques qui ont été installés.
Mecalux a installé le module de contrôle Galileo, chargé de donner les ordres aux convoyeurs, aux navettes et aux élévateurs, afin de garantir qu'ils se déplacent de manière continue et contrôlée.
Galileo possède une interface très intuitive et est capable de simuler le fonctionnement électromécanique de l’installation automatique complète par le biais d'un système SCADA.
Il est en communication permanente et bidirectionnelle avec le logiciel de gestion d’entrepôt et avec l'ERP de Nestlé. Cela a permis à l’entreprise d'optimiser la productivité de tous les processus qui se déroulent dans son centre de production.
Les avantages pour Nestlé
- Un système de transport efficace : les convoyeurs offrent une grande rapidité au déplacement de la marchandise vers les différentes zones du centre de production et l’entrepôt.
- Un flux de marchandise élevé : le circuit de convoyeurs automatiques et les élévateurs fournissent le nombre de mouvements de palettes nécessaires à Nestlé.
- Sécurité de l’installation : les éléments automatiques sont protégés pour éviter les incidents, ainsi que l’accès du personnel non autorisé.
Galerie
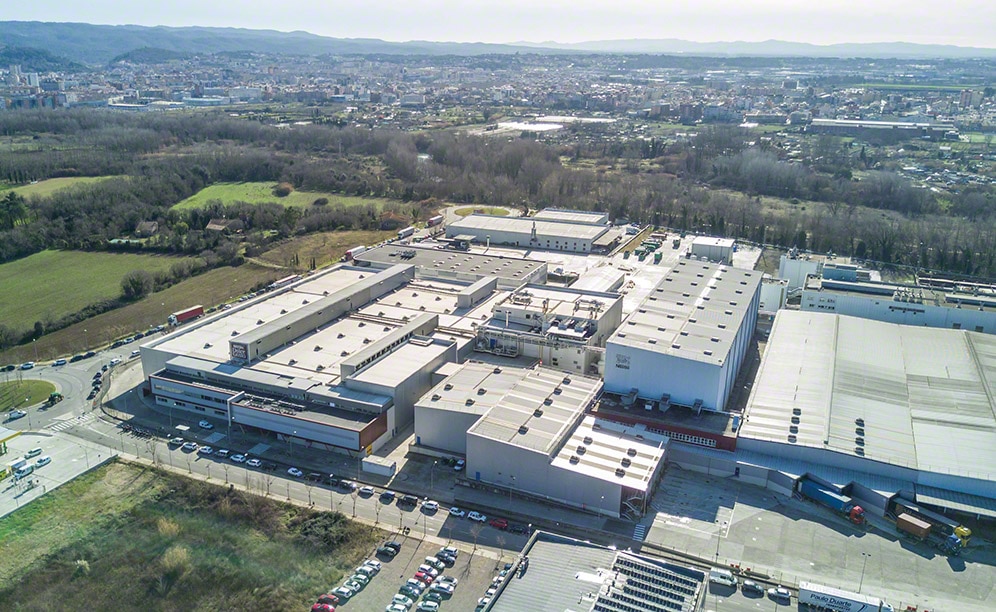
Demandez conseil à un expert