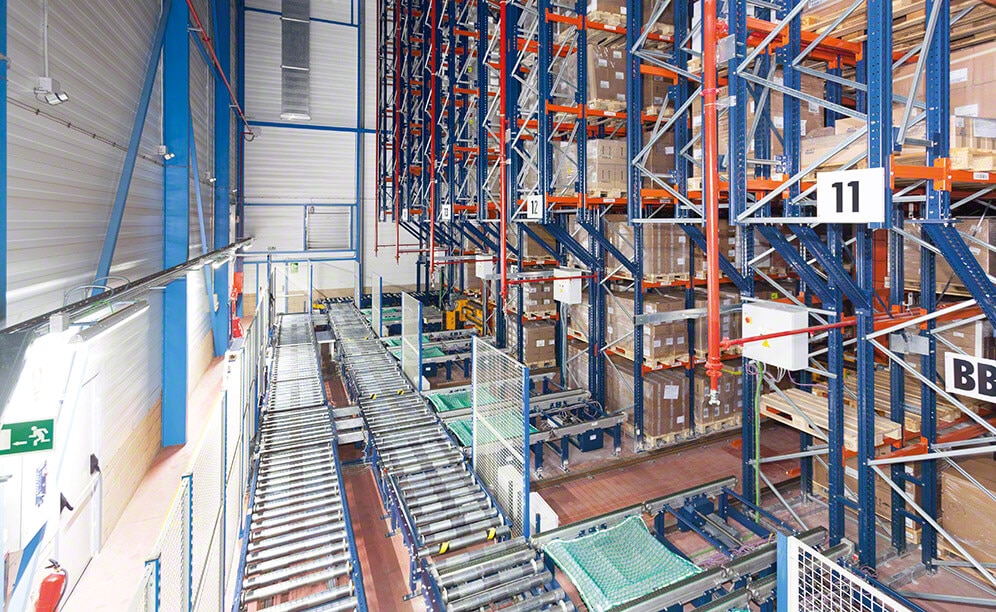
Disalfarm augmente sa capacité de stockage, la productivité et le contrôle, en automatisant les différentes zones de son entrepôt
Disalfarm automatise rapidement et à moindre coût son magasin avec des transstockeurs trilatéraux
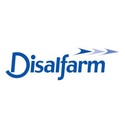
Le centre logistique de Disalfarm, situé à Rubí (près de Barcelone), a été construit sur une surface de 39 027 m². L'entrepôt est désormais entièrement automatique et il offre une capacité de stockage de plus de 19 000 palettes. Il a fortement contribué à l'amélioration des performances de Disalfarm. Aucune suspension d'activité n'a été nécessaire durant la phase d'agrandissement et de modernisation de l'entrepôt.
Présentation de Disalfarm
Disalfarm S.A. est une entreprise de logistique espagnole créée par les laboratoires Bayer, Boehringer Ingelheim et Novartis pour qu'elle puisse gérer leurs opérations nationales de stockage et de distribution de produits pharmaceutiques.
La société a démarré son activité en 2000 avec l'ambition de dominer le secteur de la distribution pharmaceutique.
Pour ce faire, il était indispensable de travailler avec un système de qualité capable de garantir les normes de bonne fabrication et distribution exigées par la législation en vigueur.
Aujourd'hui, Disalfarm dispose d'une large gamme de produits qui inclut les produits pharmaceutiques vendus sous prescription médicale, les médicaments pour usage hospitalier ou vétérinaire, les compléments alimentaires ainsi que d'autres produits sanitaires.
Sa situation géographique
Disalfarm, S.A. est situé à Rubí, une zone industrielle proche de Barcelone qui est aussi un important carrefour de communications.
Ses installations sont proches des principaux centres logistiques et de distribution, ce qui lui permet de proposer un service rapide et efficace à tous ses clients.
Les besoins de Disalfarm : se développer sans ralentir l’activité
Le niveau de croissance obtenu par Disalfarm au cours des dernières années a provoqué un changement radical de ses besoins de stockage.
En 2000, l'entreprise a fait fabriquer un centre logistique capable de combiner les opérations de stockage avec celles de picking : moins de 20 % des commandes correspondaient à des palettes complètes d'une seule référence.
Dans cette première phase, Disalfarm a fait construire deux bâtiments de stockage, une zone de préparation et de consolidation, des quais de chargement et de déchargement, mais aussi des bureaux et des toilettes.
L'ensemble de ces installations occupait une surface de 9 706 m2. Tous les rayonnages de l'entrepôt et de la zone de picking ont été installés par Mecalux.
En 2007, l'entrepôt est désormais trop petit. Le nombre élevé de mouvements réalisés par les chariots de manutention représentait un coût important et cette méthode augmentait le risque d'accidents du travail, ce qui va à l'encontre de la politique de Disalfarm.
Face à cette situation, Disalfarm a demandé à Mecalux d'améliorer ce centre logistique sans altérer le niveau de service proposé à ses clients.
Point de départ : phase 1 et phase 2
Lors de la première phase, en 2000, Disalfarm a fait construire :
- Un entrepôt d'une capacité de stockage de 12 900 palettes de 800 x 1 200 mm équipé de dix allées et de rayonnages de 15 m de hauteur.
- Une zone de picking composée de rayonnages dynamiques avec des dispositifs pick-to-light et des convoyeurs de caisses permettant de relier cette zone avec la zone d'emballage et de consolidation.
- Une zone de picking de caisses complètes directement réalisé sur les palettes.
- Un entrepôt pour produits réfrigérés de 290 palettes.
- Un entrepôt fermé pour les produits psychotropes.
- Neuf quais de chargement avec une vaste zone de manœuvre.
Dans la seconde phase, Disalfarm a fait ajouter cinq allées de plus et des rayonnages à palettes pouvant stocker jusqu'à 6 450 palettes. La capacité totale de stockage est donc passée à 19 350 palettes.
Par ailleurs, trois nouveaux quais de chargement ont été installés. Le flux de déplacements a également considérablement augmenté, jusqu'à atteindre les 1 100 palettes par jour (500 en entrée et 600 en sortie).
Pour déplacer cette quantité de palettes, les ressources suivantes étaient déployées :
- Sept chariots élévateurs frontaux pour travailler sur les quais, alimenter les zones de picking et déposer ou retirer les palettes de la zone périphérique des allées.
- Cinq chariots trilatéraux pour travailler uniquement à l'intérieur des allées de stockage.
- 24 opérateurs pour manipuler les chariots (12 par équipe).
Les deux graphiques de ce chapitre représentent les flux de mouvements (entrées et sorties) et la manière dont ils se croisent dans l'allée principale.
Flux de la marchandise dans les phases 1 et 2
La marchandise arrivait à l'entrepôt entièrement palettisée. L’opérateur lisait le code-barres de chaque palette à l’aide d’un terminal informatique et le système de gestion de l'entrepôt (WMS) lui indiquait l’emplacement assigné. Une fois que la position était déterminée, on utilisait les chariots frontaux pour transporter les palettes jusqu'aux consoles placées à l'extrémité de l’allée de stockage, afin que les chariots trilatéraux les stockent aux emplacements désignés par le logiciel Easy WMS.
Les opérations de sortie sont réalisées de manière inverse, mais la plupart des palettes étaient envoyées vers les zones de picking.
Phase 3 : supprimer le transport interne de palettes complètes
La croissance de l’entreprise n'impliquait pas une augmentation du nombre d'emplacements, c'est le mouvement des palettes qui devait être augmenté. Pour ce faire, l'entreprise pensait d'abord augmenter le nombre de chariots et le nombre d'opérateurs, avec le risque que cela implique.
L'installation disposait de quinze allées de stockage et de cinq chariots trilatéraux. Bien qu'il était possible d'introduire cinq chariots trilatéraux supplémentaires, cette solution a vite été écartée car il s'agissait là de machines semi-automatiques. Ces machines ne sont pas très rapides et le nombre de cycles offerts était donc insuffisant pour couvrir les besoins de Disalfarm.
Mecalux a alors retenu deux solutions en proposant des convoyeurs automatiques à rouleaux et à chaînes pour éliminer tous les mouvements des chariots à contrepoids dans l'entrepôt.
Première proposition de phase 3 : refusée
Une zone périphérique composée des éléments suivants apparaissait dans cette proposition :
- Deux brins principaux perpendiculaires aux rayonnages.
- Deux postes (un d'entrée et un autre de sortie) dans chaque allée de stockage.
- Un poste d'entrée et d'inspection de palettes dans la zone des quais pour rejeter les palettes qui ne conviennent pas.
- Une sortie directe vers la zone d'expéditions.
- Deux sorties vers les zones de picking.
Cette proposition était plus cohérente du point de vue de la proximité avec les quais, et elle permettait d'alimenter les postes de picking.
Pour les opérations de stockage, on aurait pu faire appel aux chariots trilatéraux et, dans le futur, augmenter le nombre de chariots ou installer une solution automatique si besoin. En plus de tout cela, la partie arrière serait destinée à la zone de changement d’allées pour les chariots trilatéraux, comme prévu dans la première phase.
Deuxième proposition de phase 3 : la solution
La partie principale de la zone périphérique devait être placée à l'arrière de l'entrepôt. De cette façon et comme cela se faisait déjà, l'allée principale pouvait servir pour les manœuvres de changement des trilatérales et pour la circulation des chariots frontaux.
Cette solution était plus complexe et plus coûteuse, elle impliquait l'installation d'un circuit de convoyeurs dans la partie inférieure de l'un des rayonnages afin de transporter toute la marchandise provenant des quais. Même problème pour les sorties, mais cette proposition pouvait être mise en place en poursuivant les opérations quotidiennes.
Les déplacements entre les postes d’entrée et les lieux d'emplacement sont réalisés par les chariots trilatéraux. Une fois la reconstruction terminée, l’allée principale était aménagée uniquement pour le changement d’allée des chariots trilatéraux et pour les quelques sorties directes vers la zone d’expédition.
Le programme de contrôle Galileo de Mecalux a alors été installé. Il permet de diriger tous les déplacements automatiques des convoyeurs, du poste d’entrées jusqu'aux sorties, en passant par la zone de picking. Les terminaux radiofréquence ont été conservés pour donner des instructions aux opérateurs des chariots trilatéraux.
Phase 4 : l'automatisation totale de l'entrepôt
Les avantages de l'automatisation des mouvements d'entrée et de sortie et aux vues des nouvelles prévisions de croissance, Disalfarm a souhaité automatiser l’ensemble de l’entrepôt.
Cependant, l'automatisation intégrale générait un nouvel inconvénient : les machines automatiques (transstockeurs) qui existent sur le marché ne permettent pas de laisser les palettes au niveau du sol. Pour y remédier, la seule option viable était de surélever le premier niveau de 60 à 70 cm au-dessus du sol et d'insérer un guide sur la partie supérieure des allées. Cette solution entraînait la perte de tout un niveau de l'entrepôt ou, ce qui revient au même, perdre 1 290 palettes.
Comme les besoins de Disalfarm ne permettaient pas une telle perte de capacité de stockage, il était nécessaire de trouver un autre type d'automatisation ou de construire un autre centre logistique.
Mecalux a alors lancé sur le marché le transstockeur trilatéral, substitut naturel des chariots trilatéraux, qui s'adaptait parfaitement aux caractéristiques du centre logistique de Disalfarm.
Ses particularités sont les suivantes :
- Il permet de laisser les palettes à 10 cm du sol.
- Il dispose de fourches trilatérales bien meilleures que les fourches télescopiques classiques.
- Aucun guide n'est requis dans la partie supérieure des allées, il n'a besoin que de deux guides au sol.
- Sa hauteur maximale est de 15 m.
- Il peut porter un pont de transbordement (pour les changements d’allées).
- Il est compatible avec le programme de contrôle Galileo.
- Il offre au moins la même capacité de stockage que les trilatéraux.
Les changements réalisés lors de la phase 4
Les changements appliqués étaient minimes et simples d'exécution :
- Installer les deux guides au sol.
- Modifier légèrement les hauteurs entre les niveaux.
- Prolonger le poste de contrôle installé sur les convoyeurs de la zone périphérique.
Installer des grilles de sécurité pour adapter toute l’installation aux normes d'automatisation des entrepôts, surtout si elles ont un rapport avec la sécurisation des allées où passent les transstockeurs.
Les entrées des allées concernées par les opérations de maintenance de l'entrepôt sont effectuées par le côté opposé de la zone périphérique, c'est-à-dire, là où était située l'allée principale de l'installation lorsque l'entrepôt fonctionnait avec des chariots trilatéraux.
Pour les quelques opérations de sortie de palettes complètes, un canal dynamique a été installé dans chaque allée sur les consoles de la zone périphérique antérieure. Il est accessible avec des chariots à contrepoids, sans avoir à entrer dans les zones de déplacements automatiques.
La communication avec le logiciel
Disalfarm disposait dès le départ d'un système de gestion d'entrepôt (WMS) puissant et adapté à ses besoins. Continuer à utiliser ce système pour gérer tout l’entrepôt était une condition obligatoire. Mecalux a donc installé son programme de contrôle standard. Le système de contrôle Galileo gère tous les mouvements à l'intérieur de l'entrepôt. De même, une interface de communication a été développée pour que les deux systèmes communiquent correctement, ainsi qu’une couche intermédiaire de gestion pour éviter les incohérences de réservations et d'occupation des emplacements.
Les avantages pour Disalfarm
- Une grande capacité de stockage dans un espace réduit : l'entrepôt de Disalfarm permet de stocker 19 350 palettes de 800 x 1 200 mm.
- Une amélioration sans réduction d'activité : Mecalux a optimisé le centre logistique de Disalfarm sans aucun arrêt d'activité en restant dans les mêmes installations.
- Une productivité élevée : l’automatisation des différents processus de stockage a augmenté le flux de mouvements pour répondre aux besoins de l'entreprise.
- Un contrôle total : l'interface de communication entre le système de gestion d'entrepôt de Disalfarm et le programme de contrôle standard de Mecalux permet de gérer les processus et opérations qui se déroulent dans l'entrepôt.
Centre logistique de Disalfarm | |
---|---|
Capacité de stockage: | 19 350 palettes |
Dimensions des palettes: | 800 x 1 200 mm |
Poids max. / palette: | 800 kg |
Hauteur des rayonnages: | 13 m |
Longueur des rayonnages: | 60 m |
Nb. de transstockeurs: | 15 |
Type de transstockeur: | trilatéral automatique |
Galerie
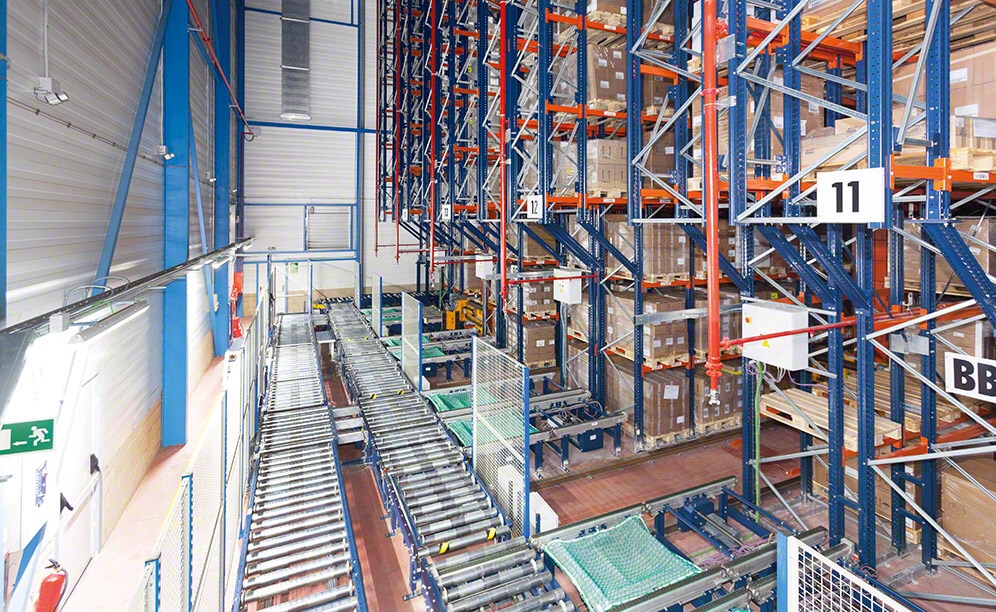
Demandez conseil à un expert