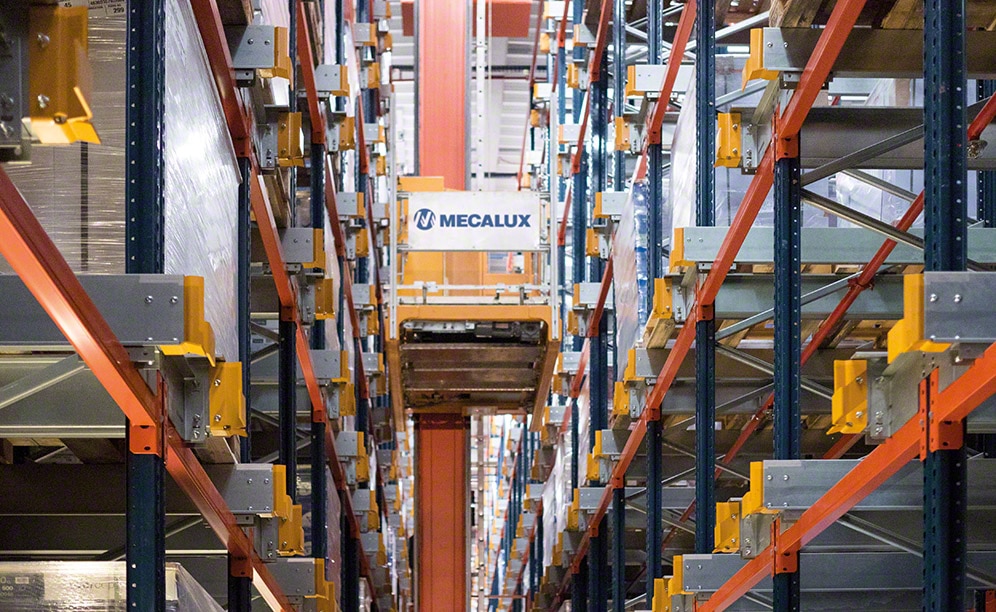
Haute performance dans les entrepôts automatisés de Clairefontaine en France
Le fonctionnement de l'entrepôt est entièrement automatique, entraînant une intervention minimale des opérateurs.
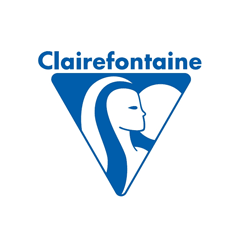
Clairefontaine, le fabricant français spécialisé dans la papeterie, a intégré les dernières technologies dans son processus logistique et a également agrandi son entrepôt situé dans les Vosges (France). Il fonctionne de manière entièrement automatisée, ce qui requiert une intervention minimale des opérateurs. Mecalux a participé à ce projet, dès son commencement, en concevant et en essayant de mettre en œuvre les solutions les plus efficaces. Ces dernières ont aidé l’entreprise à consolider sa position de leader dans le secteur ainsi qu’à renforcer ses perspectives de croissance future.
À propos de Clairefontaine
L’entreprise est l’une des structures spécialisées dans la fabrication de papiers et de produits dérivés les plus anciennes de France. Outre sa production allant jusqu’à 170 000 tonnes par an, son catalogue de produits inclut des papiers pour bureautique, imprimeurs et transformateurs.
Cette entreprise a été créée en 1858, dans la ville d'Étival-Clairefontaine, profitant ainsi de son emplacement au bord de la Meurthe. Très vite, elle est devenue l'une des industries les plus importantes de la région. Elle se distingue par sa capacité d'adaptation aux changements du marché et par l’intégration des dernières technologies dans l’ensemble des processus de production.
Elle fait partie d’Exacompta Clairefontaine, un groupe qui comprend plus de 50 entreprises productrices de papier en Europe. Ces dernières années, elle a misé sur la rénovation et la modernisation de toutes les installations de ses entreprises afin d'augmenter la productivité.
Le centre logistique
Compte tenu de la stratégie d'entreprise du groupe, Clairefontaine a réorganisé le fonctionnement de son centre logistique dans les Vosges, d'où elle distribue toute la marchandise à ses clients de par le monde.
L'entreprise avait besoin d’obtenir une grande capacité de stockage tout en fournissant un service rapide et efficace. L’équipe technique de Mecalux a collaboré étroitement avec celle de Clairefontaine, afin de concevoir la solution la plus efficace pour répondre à ses besoins logistiques.
Après une étude minutieuse, le résultat obtenu est un centre logistique composé de trois entrepôts avec un processus opérationnel entièrement automatisé.
Parmi les avantages de cette solution, soulignons un contrôle précis des produits, un accroissement de la productivité et une importante disponibilité, puisque ce système fonctionne en continu, 24h/24, 7j/7. Il permet aussi de limiter les frais de personnel (mettant un terme à la dépendance aux engins de manutention traditionnels) et les coûts d'exploitation.
Le centre est situé sur une grande parcelle de terrain. Transporter la marchandise du centre de production aux entrepôts assignés pouvait entraîner un coût de manutention très élevé, ce qu'il convenait de minimiser. En conséquence, l'entreprise a opté pour automatiser également le transport interne. Les produits finis, provenant du centre de production, sont stockés dans l'un des trois entrepôts en fonction de leurs caractéristiques et de leur rotation :
- Entrepôt doté du système Pallet Shuttle automatique.
- Entrepôt automatisé pour picking.
- Entrepôt doté de chariots trilatéraux automatiques.
Florian Challe - Responsable d’Exploitation Logistique
« Mecalux a mis en œuvre trois solutions de stockage adaptées à nos différents flux. L’automatisation nous a permis d’améliorer nos performances et notre réactivité tout en réduisant les coûts d’exploitation et les dommages occasionnés sur nos produits. »
Transport automatisé
Au commencement de ce ambitieux projet, Clairefontaine avait proposé d'automatiser au maximum toutes les opérations de son centre logistique, y compris le transport interne, grâce à l'installation de véhicules autoguidés (AGV).
Les chariots AGV exécutent les fonctions qui, dans un entrepôt non automatisé, seraient réalisées par les opérateurs à l'aide de chariots traditionnels, comme le transfert de la marchandise du centre de production à l'entrepôt.
L'utilisation de ces chariots permet de disposer d’espaces et d'allées de circulation entièrement libres.
Pour arriver à l'entrepôt équipé du système Pallet Shuttle automatique – qui est le plus éloigné –, une allée a été ouverte sur l'un des côtés de l’entrepôt. Seules les machines AGV circulent à cet emplacement.
Entrées et sorties du centre logistique
La plupart des palettes provenant de l’atelier de production sont de dimensions non standard. Elles sont donc placées sur des palettes esclaves afin de garantir la résistance des charges et leur stabilité à l'intérieur de l'entrepôt.
Un circuit de convoyeurs, avec un remonteur à palettes qui dépose la marchandise sur les palettes esclaves, a été installé pour réaliser cette opération.
Toutes les palettes passent alors obligatoirement par la zone d’inspection : on s’assure de leur bon état et on vérifie également que leur poids et leurs dimensions correspondent aux données théoriques. La marchandise, quittant l’entrepôt et se dirigeant par la suite vers les expéditions, est réintroduite dans le circuit de convoyeurs.
À cette occasion, la palette esclave est récupérée pour être utilisée ultérieurement avec de nouvelles charges provenant de la production.
Zone de préchargement
Les palettes, quittant l'entrepôt, sont transportées jusqu’à la zone de préchargement située en face des quais de chargement. Elles y sont regroupées à l’avance par commande ou par itinéraire afin de pouvoir être chargées dans les camions en un temps réduit.
Entrepôt doté du système Pallet Shuttle automatique
Cet entrepôt est destiné à des produits à forte rotation. Le Pallet Shuttle est un système par accumulation qui offre une capacité de stockage optimale et qui accélère l'entrée et la sortie des palettes à l'aide de navettes autonomes. Ce système est la solution la plus efficace lorsqu’on est en présence d’une quantité importante de palettes par référence et lorsqu’il s’agit de produits à forte rotation.
L'entrepôt, de 15 m de haut et de 146 mètres de long, dispose de trois allées avec un bloc de rayonnages de part et d'autre qui accepte entre cinq et sept palettes en profondeur. Les palettes, dont le poids maximum est de 900 kg, mesurent 800 x 1 200 mm, et présentent quatre hauteurs différentes : 1 095 mm, 1 395 mm, 1 645 mm ou 1 745 mm.
La distribution de la marchandise tient compte de ces dimensions en consacrant les niveaux inférieurs aux palettes de petites dimensions et les niveaux supérieurs à celles présentant une plus grande hauteur. La capacité de stockage totale obtenue est de 20 611 palettes.
Cette version du système Pallet Shuttle est entièrement automatisée, elle utilise, en effet, trois transstockeurs (un par allée) comme engins de transport depuis les positions d'entrée et de sortie de l'entrepôt jusqu’aux canaux de stockage.
Les navettes automatiques sont logées dans la nacelle du transstockeur et, lorsqu'elles atteignent le canal correspondant, elles élèvent légèrement la palette et l’introduisent à l'intérieur, en se déplaçant sur les rails et ce, jusqu'à arriver au premier emplacement libre.
Par la suite, elles descendent la palette et l’appuient sur la partie supérieure du rail même. Cette même opération est effectuée dans l'ordre inverse pour retirer la marchandise.
Entrepôt automatisé pour picking
Il est composé d'une seule allée de 93 m de long avec des rayonnages à palettes à simple profondeur de part et d'autre. Ils comprennent quatre niveaux fournissant une capacité de stockage globale de 744 palettes sur 7,6 m de haut. Les références nécessaires pour effectuer les tâches de picking se trouvent dans cette partie de l’entrepôt.
Un transstockeur mono-colonne, circulant dans l’allée de stockage, est chargé de déplacer la marchandise entre les convoyeurs d’entrée et de sortie, situés à une extrémité de l’allée, et les emplacements de stockage. Cette machine fonctionne à une vitesse de déplacement de 180 m/min et 38 m/min en levage, avec un potentiel supérieur aux besoins et aux prévisions futures de Clairefontaine. Deux postes de picking en forme de « U » ont été installés à l'une des extrémités des rayonnages. L’organisation de cette zone est effectuée par une navette qui distribue les palettes, provenant de l'entrepôt, à chacun des postes.
Les postes de picking disposent des équipements nécessaires pour faciliter les opérations comme des terminaux informatiques ou des tables qui élèvent les palettes jusqu’à une position plus ergonomique. L’opérateur recueille les caisses directement sur la palette d’origine (provenant de l'entrepôt) et les dépose sur les palettes de destination (commandes).
La zone de consolidation se trouve près des postes de picking : on y vérifie les commandes terminées, on emballe les palettes et on effectue également l'étiquetage et l'émission de la documentation nécessaire pour leur expédition.
Afin de protéger les opérateurs et les produits stockés, l’entrepôt automatisé et les postes de picking sont protégés par des grillages métalliques dotés d'une porte d’accès sécurisé.
Entrepôt doté de chariots tridirectionnels automatiques
Sept allées ont été aménagées avec des rayonnages à palettes de part et d'autre. Les produits à faible rotation, ainsi que les produits spéciaux demandés expressément par un client sont stockés dans ces rayonnages.
Les allées mesurent 1,8 m de large. La surface disponible de l’entrepôt a été optimisée pour offrir une capacité de stockage de 5 985 palettes. Ce système autorise l’accès direct à l’ensemble des palettes, permettant ainsi d’accélérer la gestion de la marchandise.
Deux chariots tridirectionnels automatiques sont utilisés pour manipuler la marchandise. Ceux-ci fonctionnent uniquement à l’intérieur des allées, en introduisant et en retirant les palettes de leurs emplacements. Les chariots AGV approchent ou retirent la marchandise des extrémités des allées.
Un logiciel intelligent
Face à l'envergure et à la complexité de ce projet, Clairefontaine avait besoin d’un logiciel efficace de gestion d’entrepôt (WMS) capable de piloter toutes les opérations internes.
Mecalux a mis en place Easy WMS, un logiciel chargé de contrôler et de coordonner tous les processus logistiques, ainsi que de rentabiliser les opérations des différents entrepôts. Il est capable d'exécuter les fonctions suivantes :
- Contrôle total de la gestion de l'entrepôt.
- Gestion de l’entrée et sortie de la marchandise.
- Assignation d’un emplacement destiné aux produits selon leurs caractéristiques et leur rotation.
- Organisation de l’ordre de sortie de la marchandise.
- Optimisation de la préparation des commandes.
Easy WMS de Mecalux est en communication permanente et bidirectionnelle avec le système de planification de ressources de Clairefontaine : il transfère des données et des informations fondamentales afin de connaître en temps réel l'état de l'inventaire.
S'agissant d'un entrepôt entièrement automatisé, Mecalux a également installé le module de contrôle Galileo, qui garantit le bon fonctionnement de tous les éléments électromécaniques du centre logistique et le respect des mesures de sécurité.
Les avantages pour Clairefontaine
- Une plus grande capacité de stockage : grâce à la rénovation de son centre logistique, Clairefontaine a obtenu une capacité de stockage de 27 340 palettes.
- Une gestion automatique :les entrepôts automatisés offrent un flux constant de marchandise et un système rapide pour préparer les commandes, avec une intervention minimale des opérateurs.
- chaque produit est déposé dans l'entrepôt correspondant en tenant compte de ses caractéristiques et de sa rotation.
Entrepôt avec tridirectionnels automatiques | |
---|---|
Capacité de stockage: | 5 985 palettes |
Dimensions de la palette: | 800 x 1.200 mm |
Poids max. par palette: | 900 kg |
Hauteur de l'entrepôt: | 8 m |
Longueur de l'entrepôt: | 110 m |
Nbre d’allées de stockage: | 8 |
Galerie
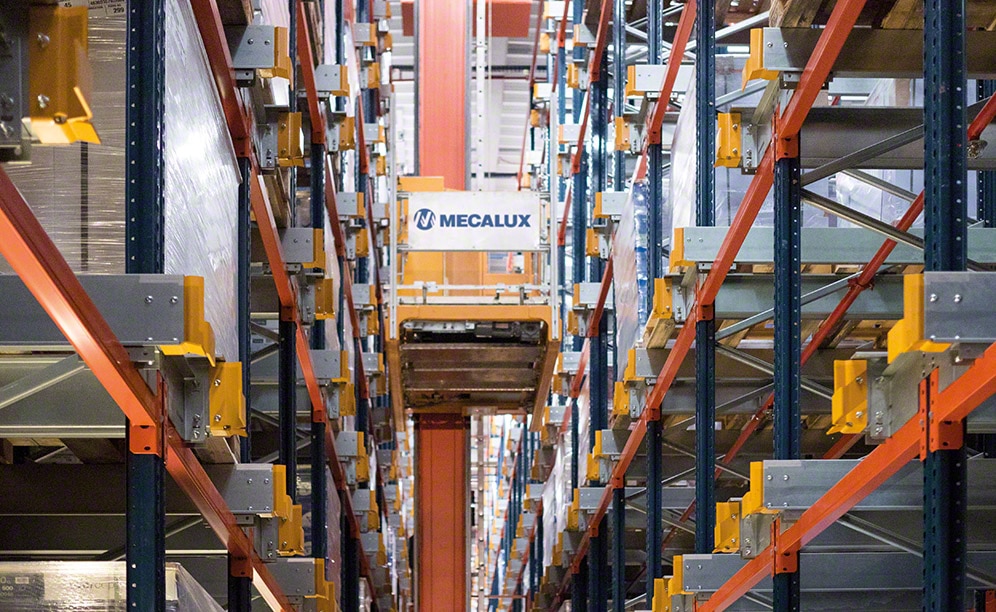
Demandez conseil à un expert