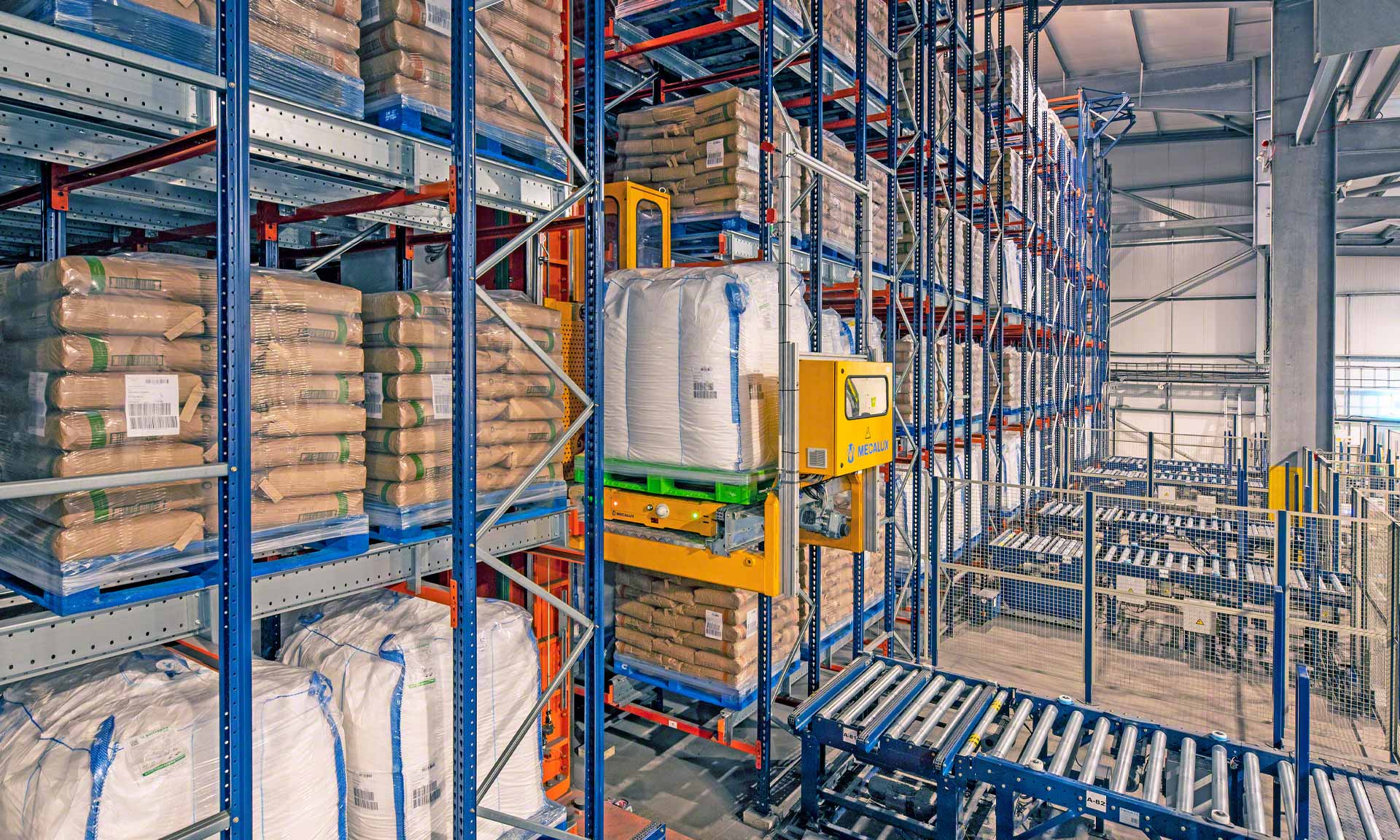
British Sugar réaffirme son engagement envers l’innovation avec un entrepôt automatisé à Wissington
British Sugar, le principal sucrier au Royaume-Uni, installe un entrepôt automatisé Mecalux dans la plus grande usine de sucre en Europe.
British Sugar, le principal sucrier au Royaume-Uni, optimise la logistique de son usine de Wissington avec un magasin automatique pour palettes. Piloté à l’aide du logiciel de gestion Easy WMS, l’entrepôt est relié aux lignes de production de manière automatique.
British Sugar : premier producteur de sucre
British Sugar est le principal producteur de sucre en Grande-Bretagne et en Irlande. L’entreprise ne cesse de se développer, elle a investi plus de 280 millions d’euros ces dernières années pour doubler sa capacité de production. British Sugar fait partie d’AB Sugar, détenue à 100 % par la multinationale agroalimentaire Associated British Foods (ABF).
- Année de création : 1912
- Sites de production : 4
- Capacité de production : 1,2 million de tonnes de sucre
- Effectif : 1 400
DÉFIS
|
SOLUTIONS
|
AVANTAGES
|
---|
Si British Sugar est capable de répondre à environ la moitié de la demande de sucre au Royaume-Uni, et ce de manière efficace et faisant face aux changements du marché, c’est grâce à son pari sur l’innovation et la technologie.
Ces dernières années, l’entreprise britannique a mis en œuvre un projet de modernisation de ses quatre sites de production pour devenir plus compétitive et offrir un excellent service à ses clients. British Sugar a conclu un accord avec l’opérateur de télécommunications Virgin Media O2 pour interconnecter quatre de ses usines à l’aide de la 4G. Le but ? Renforcer l’automatisation et l’internet des objets (IoT) en vue de créer un environnement de travail numérique plus sécurisé.
À Wissington (Royaume-Uni), British Sugar possède la plus grande usine de transformation du sucre d’Europe. Depuis son ouverture en 1925, l’installation a été transformée année après année pour devenir la première usine de production de bioéthanol du pays. « Aujourd’hui, l’usine transforme plus de 3 millions de tonnes de betteraves sucrières par an en 400 000 tonnes de sucre destinées à la consommation humaine et 64 000 tonnes d’éthanol (utilisé dans la production d’énergie motrice ou électrique) », explique Samuel Chapman, directeur des achats de British Sugar.
Avec un tel rythme de production et des perspectives de croissance future très prometteuses, l’entreprise était à la recherche d’un système de stockage capable de stocker les 1 500 palettes de produits finis quotidiennes. Auparavant, British Sugar déposait les marchandises sur des racks à palettes à capacité insuffisante. « Le stockage étant manuel, les opérateurs passaient beaucoup de temps à charger et décharger les palettes », explique Samuel Chapman.
Après avoir évalué différentes solutions, le producteur de sucre a opté pour l’automatisation. La solution de stockage choisie est le Pallet Shuttle avec transstockeurs de Mecalux, un système qui optimise la surface disponible pour stocker un maximum de produits. « La circulation de marchandises est automatisée, ce qui accélère les entrées et sorties. Grâce au déplacement automatique des transstockeurs, convoyeurs et navettes motorisées, nous pouvons assurer le nombre de cycles nécessaire pour servir nos clients », explique Samuel Chapman.
Michael Burton, responsable approvisionnement à l’usine British Sugar de Wissington, explique pourquoi l’entreprise a misé sur les nouvelles technologies : « L’innovation est présente dans l’ensemble de notre activité, elle est fondamentale pour l’avenir de nos usines. C’est pourquoi nous cherchons l’amélioration continue de nos opérations et, en particulier, à optimiser notre entrepôt. Cela est essentiel pour répondre aux besoins de nos clients et pour devenir leur fournisseur privilégié ».
Burton ajoute que « le fait d’avoir un seul et même fournisseur comme Mecalux pour les solutions de stockage automatisées comme pour le logiciel a été non seulement très avantageux pendant la phase de conception et de mise en service, mais aussi il a signifié une aide précieuse une fois le système opérationnel ».
Caractéristiques de l’entrepôt automatisé
« Les opérations logistiques sont au cœur de la stratégie commerciale de British Sugar. Nous sommes le fournisseur choisi par nos clients, nous devons donc optimiser notre chaîne d’approvisionnement, et la logistique en est un élément clé », déclare Samuel Burton.
Le nouvel entrepôt, relié à la production de manière automatique par un circuit de convoyeurs pour palettes, reçoit 1 500 palettes de produits finis par jour. Elles doivent passer une inspection pour vérifier leurs dimensions et poids.
Le circuit de convoyage, qui connecte les lignes de production avec la zone de stockage, longe la partie latérale des rayonnages pour atteindre l’avant de l’entrepôt automatisé. « La communication automatique entre les deux installations est essentielle pour accélérer le flux des marchandises », souligne Samuel Burton.
Le Pallet Shuttle est un système de stockage compact entièrement automatisé où une navette motorisée déplace les palettes à l’intérieur des canaux de stockage en toute autonomie. Dans chacune des six allées, un transstockeur transfère les marchandises des positions d’entrée de l’entrepôt vers n’importe quel canal de stockage, en suivant les instructions du logiciel de gestion d’entrepôt Easy WMS de Mecalux.
« L’automatisation nous a apporté de nombreux avantages, notamment l’amélioration des conditions de travail des opérateurs, résultant d’une moindre circulation de chariots élévateurs dans l’entrepôt », se réjouit Samuel Burton.
Les rayonnages exploitent au mieux la surface de l’entrepôt de manière à maximiser la capacité de stockage. Ainsi, l’entrepôt de British Sugar peut contenir 4 500 palettes sur environ 4 200 m².
Grâce à l’automatisation, British Sugar a atteint le rythme de travail souhaité pour pouvoir expédier 1 500 palettes de produits finis par jour à ses clients au Royaume-Uni et ailleurs en Europe. Cela est possible grâce aux quatre points d’expédition de marchandises installés par Mecalux. Ces derniers consistent en un circuit de convoyage automatique reliant l’entrepôt à la zone des quais de chargement, situés juste devant les rayonnages pour accélérer la distribution des marchandises.
Les équipements de manutention automatiques de l’entrepôt de British Sugar (convoyeurs, transstockeurs et navette Pallet Shuttle) assurent le traitement efficace et sans erreurs de 3 000 palettes par jour (1 500 entrantes et 1 500 sortantes).
Un entrepôt sous contrôle numérique
Pour contrôler les nombreuses références et la forte circulation quotidienne de marchandises, le système de gestion Easy WMS de Mecalux a également été mis en œuvre dans l’entrepôt. « En tant que fournisseur privilégié, il est fondamental pour nous d’assurer une traçabilité totale de nos stocks. Easy WMS offre une analyse approfondie de chaque produit, nous avons ainsi accès à l’historique complet et provenance de toute palette dans l’entrepôt », explique Samuel Burton.
Le logiciel utilise des règles et des algorithmes pour organiser les produits en fonction de leurs particularités et du niveau de la demande. Chaque allée est divisée en trois secteurs selon la rotation des articles, de type A, B ou C. Ainsi ceux de type A (haut niveau de demande), par exemple, sont déposés à l’avant des rayonnages pour accélérer les entrées et les sorties, ceux de type B ou C occupant les emplacements les plus éloignés.
Pour améliorer la gestion des marchandises, le logiciel de gestion d’entrepôt communique avec l’ERP de British Sugar. Ce dernier notifie à l’avance à Easy WMS la réception d’articles provenant de la production, afin que les emplacements puissent être attribués rapidement.
Logistique 4.0
« British Sugar est une entreprise très dynamique, nous sommes donc obligés d’avoir une certaine flexibilité quant à nos systèmes de stockage et au niveau de l’usine de production, de sorte qu’on puisse traiter les fluctuations efficacement et sans effort », déclare Samuel Burton.
British Sugar est une entreprise innovante qui a depuis ses débuts misé sur la technologie dans le but de favoriser les changements et l’amélioration continue de ses processus. L’inauguration de ce nouvel entrepôt dans son usine de Wissington témoigne de l’avenir prometteur de producteur de sucre.
L’automatisation et la numérisation servent à British Sugar de leviers pour atteindre ses objectifs. La technologie lui permet un contrôle strict des produits et des opérations optimisés. Le tout ayant un but bien défini : offrir des produits de qualité.
La mise en service d’un nouvel entrepôt automatisé fait partie de notre stratégie d’optimisation de la chaîne d’approvisionnement. Grâce à la technologie et à la robotique, nous espérons avoir un contrôle précis des produits et accélérer le stockage et l’expédition des commandes.
L’automatisation des systèmes de stockage Mecalux nous a apporté de multiples avantages logistiques, notamment en matière d’amélioration des conditions de travail du personnel. La gestion avec Easy WMS nous offre quant à elle une traçabilité totale de nos stocks, ce qui est indispensable dans notre métier.
Galerie
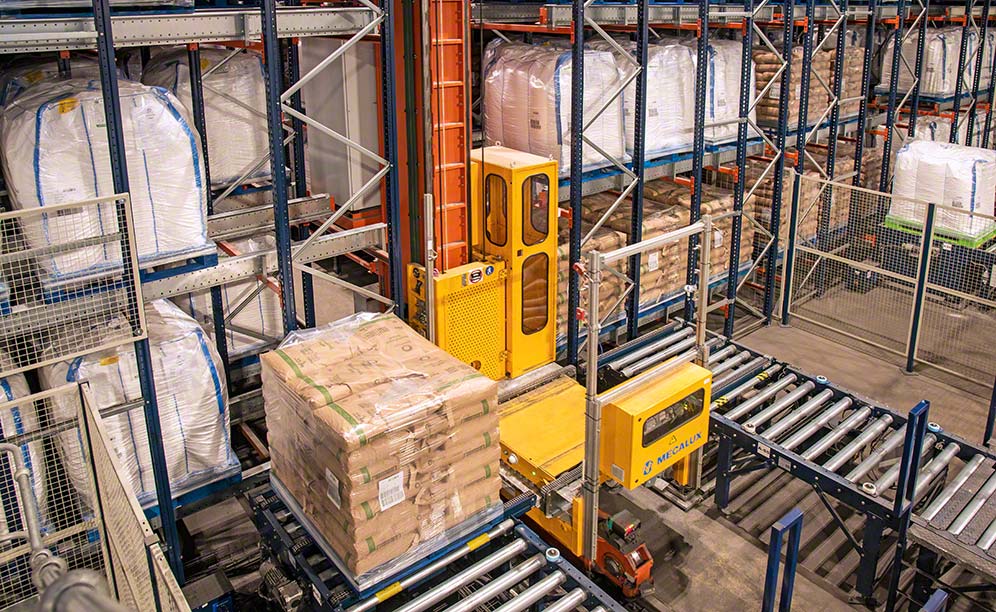
Le transstockeur déplace les palettes dans les allées de stockage
Demandez conseil à un expert