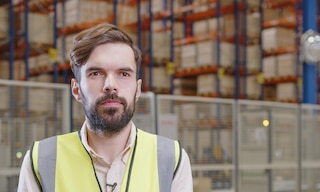
Entretien avec Pavol Masarovič, directeur des opérations de IKEA Components Slovaquie
« L’automatisation de l’entrepôt a été achevée sans interrompre les opérations »
À propos d’IKEA Components
IKEA Components, filiale de la multinationale suédoise IKEA en charge de l’emballage et de la livraison des accessoires et composants de meubles, a modernisé son entrepôt de Malacky, en Slovaquie, en y installant des transstockeurs tridirectionnels sans jamais interrompre l’activité. Le logiciel de gestion Easy WMS a également été mis en œuvre afin d’accroître l’efficacité.
Mecalux a interviewé Pavol Masarovič, directeur des opérations de IKEA Components Slovaquie. La filiale a automatisé son entrepôt de Malacky (Slovaquie) sans jamais interrompre les opérations et a également gagné en capacité de traitement des commandes.
-
IKEA est présent sur 62 marchés et possède plus de 450 magasins. Comment décririez-vous la logistique de IKEA Components avant l’automatisation ?
Auparavant, l’ensemble de notre zone d’expédition fonctionnait de manière purement conventionnelle. Autrement dit, tous les déplacements et transferts de palettes étaient réalisés manuellement, à l’aide de chariots élévateurs ou dans des rayonnages à allées étroites. Nous acheminions les palettes depuis la zone de production et les stockions dans l’entrepôt. Cette façon de travailler demandait beaucoup de temps, de matériel et de main d’œuvre, c’est pourquoi nous avons décidé d’automatiser certains processus pour gagner en efficacité.
-
Mecalux a automatisé l’entrepôt d’IKEA Components à Malacky sans interrompre les opérations. Comment s’est déroulé le projet ?
La principale exigence posée à Mecalux a été de planifier et de concevoir l’ensemble du projet de manière à ne pas perturber nos activités pendant l’installation. Une exigence que nous avons formulée avant même de démarrer les travaux. La fermeture complète de l’entrepôt n’était en effet pas envisageable.
Le projet a été divisé en quatre phases. Dans chacune d’elles, trois transstockeurs tridirectionnels étaient installés et le circuit de convoyage étendu. Cette répartition des travaux nous a permis de les achever avec une incidence de 25 % seulement sur la capacité totale au cours de chaque phase. Les travaux n’ont donc eu qu’un faible impact et n’ont pas affecté notre activité quotidienne.
Nous nous concentrons désormais sur les stocks, les équipements automatiques s’occupant du déplacement des palettes
-
Quels avantages l’entrepôt automatisé a-t-il apporté à IKEA Components ?
L’automatisation nous offre une plus grande flexibilité et efficacité, notamment dans les mouvements de palettes. Alors qu’avant nous étions obligés de tout faire manuellement, nous n’avons plus à nous préoccuper des déplacements de palettes puisque ce sont les équipements automatiques qui les prennent en charge pour nous. Avec le stockage automatisé, nous pouvons nous concentrer davantage sur la gestion des stocks, avec une meilleure visibilité et moins d’erreurs grâce au contrôle via Easy WMS.
Le système est facile à piloter car il est géré par le logiciel de gestion d’entrepôt Easy WMS. Le programme dirige tous les processus et transmet les instructions nécessaires à la livraison des marchandises à nos clients. Les palettes quittent alors l’entrepôt en toute autonomie.
Nous avons constaté les avantages des systèmes de stockage automatisés, en particulier durant la pandémie. Malgré les arrêts maladie de certains collègues, nous avons pu continuer à répondre aux demandes de nos clients et à expédier toutes les palettes demandées, grâce au fait que le fonctionnement de l’entrepôt repose moins sur les opérateurs.
-
Quel est le parcours d’une palette de son entrée à sa sortie de l’installation ?
L’installation a été achevée avec une incidence de 25 % seulement sur la capacité totale au cours de quatre phases Toutes les palettes qui entrent dans l’entrepôt de distribution proviennent de notre zone de production, elles sont transportées par des véhicules autoguidés depuis notre point de cerclage de palettes. Ensuite, elles poursuivent leur chemin le long d’un tapis roulant et traversent le poste d’inspection d’entrée (PIE) installé par Mecalux. À cet endroit, Easy WMS sélectionne l’une des douze allées de stockage et l’emplacement de la marchandise, puis lance son transfert. Par la suite, lorsque la palette est demandée et que nous devons l’expédier à un client, le processus est automatiquement exécuté dès qu’un opérateur en donne l’ordre. Enfin, les palettes sont acheminées sur l’un ou l’autre des tapis roulants en fonction de leur destination finale et rejoignent les différentes zones de chargement par le chemin le plus court possible.
-
Quel bilan faites-vous de cette transformation intralogistique ?
Le projet de Malacky a duré presque trois ans, nous avons été confrontés à de nombreux défis mais nous les avons tous relevés de manière très professionnelle et sans nous éloigner de notre objectif principal : gagner en efficacité. La collaboration avec Mecalux a fait preuve d’un grand professionnalisme, la relation a été très cordiale et nous avons finalement accompli notre mission avec succès. De nombreuses personnes ont été impliquées, tant de leur côté que du nôtre. En somme, ce projet a été un grand succès pour nous tous – il nous a permis d’apprendre mais aussi d’acquérir des compétences et de l’expérience que nous pourrons mettre à profit à l’avenir.